The growing adoption of electric vehicles (EV) coupled with commercial demands is spurring the development of more powerful and long-lasting batteries. Between faster charging time, longer range, lower cost, and safety, the evolution of EV batteries is hot – in a both a literal and figurative sense. EV manufacturers must surmount the cooling barrier to achieve their goals, which means finding cooling solutions that account for thermal efficiency, temperature uniformity, size, weight, and cost. Similar cooling needs ring true for e-motors, as more power is making its way into the electric space, fast. In their pursuit, many cooling techniques have been explored, including air cooling, liquid cooling, and phase change materials, with liquid cooling claiming the title as today’s solution of choice for both EV batteries and e-motors as per its performance to weight and size ratio.
Diabatix is responding to today’s EV cooling challenges with an innovative approach to thermal design. By leveraging artificial intelligence in our thermal design process, we have discovered that the key to high performance cooling is in the harmonious collaboration between man and machine.
“By using AI in our generative thermal design approach, we are able to create and simulate thousands of iterations of a design in a matter of days, fully autonomously. To fully grasp the scale and speed at play here, in the time it takes a thermal engineer to create one design, we’ve already created 1 000. Think of it this way, our artificial intelligence only stops designing once its reached the optimal thermal solution”, says Diabatix CEO, Lieven Vervecken.
For EVs, Diabatix has experience designing cooling solutions for e-motors and high energy dense batteries. In this piece, three of our high performance design examples for EV cooling will be presented. One will cover e-motor cooling, and the other two focus in on high energy dense battery cooling.
Cooler, more powerful e-motors
In addition to working with multiple OEMs, Diabatix is one of the main partners for the development of the Team Delft University of Technology race car, where we developed an e-motor cooling jacket. In terms of thermal efficiency, which is one of the most important facets of e-motor cooling, our cooling jacket reduced motor temperatures by 21% and battery power drain by 80%.
Jelle Vanton, an AI engineer at Diabatix, worked on the development of the highly performant cooling jacket. “Thermal efficiency is a very important factor in the design of an electric motor. In most cases, it’s the most important factor. The more efficient a motor is cooled, the more efficient the motor will run. If the temperature of the copper windings rises, the resistance of the windings increases and the efficiency decreases. The bearings and the lubrication are also negatively affected by high operating temperatures. Maintaining low temperatures results in a long and powerful life of an electric motor”, states Vanton.
We were able to achieve these results due to the design freedom that our AI approach provides. A conventional thermal design for an e-motor is spiral like, and typically faces a higher than desired pressure drop. Since we aren't bound by a shape constraint in our unique design approach, the shape freedom that we have results in very organic patterns that remain fully manufacturable with today’s standard and experimental techniques, from die casting to sheet metal forming to 3D printing, and the like. These organic patterns are uniquely designed by artificial intelligence, with one design never resembling another.
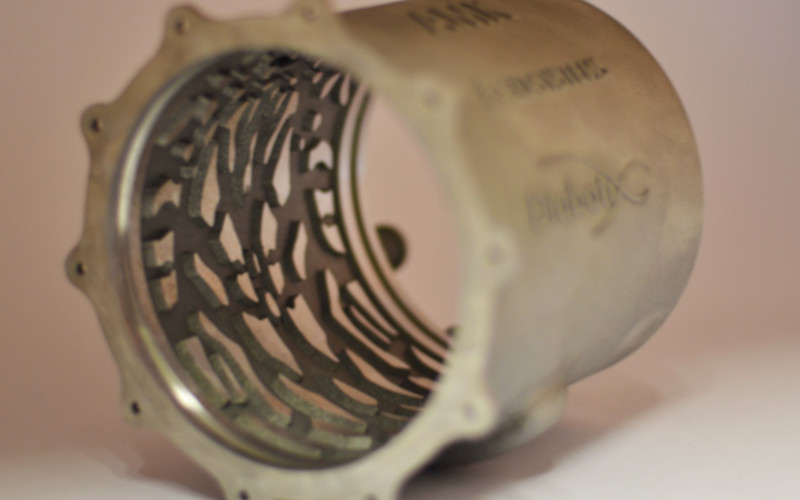
Enabling high energy dense batteries
High energy dense lithium-ion batteries allow EVs to increase their payload capacity and range, while also decreasing cost – an essential point for the continual growth of the EV market. Cooling these batteries, however, has acted as a strong barrier against increasing their power even more.
High energy dense lithium-ion batteries have the disadvantage in the sense that they produce more heat over the same surface area that their predecessors had. “It’s always a challenge to cool more powerful battery cells without having the extra surface”, comment Vanton. “The cooling then has to be far more efficient and very uniform. In cases where the pressure drop must remain virtually constant, a conventional s-shaped thermal design does not suffice”.
We are breaking down these cooling barriers with our AI driven approach. In the following comparison, one can see both a Diabatix designed liquid cooled heat sink and a conventional liquid cooled heat sink for an EV battery. In terms of results, our design performs notably better.
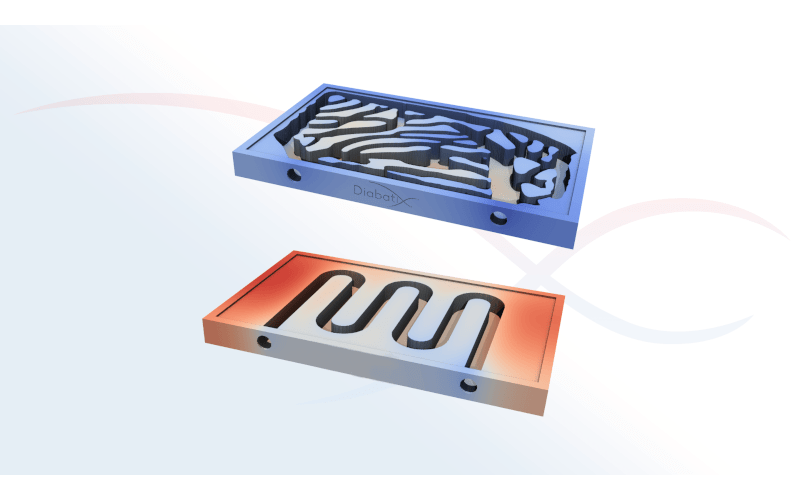
In Diabatix’s design,
- Thermal resistance was decreased by 25%
- Temperature uniformity was improved by 15%
- Pressure drop was reduced by 50%
Our AI driven approach results in designs that output higher performance to cool higher powered batteries without having to increase surface. This plays a very important role in terms of material cost.
Cutting costs by reducing weight
An additional importance to cost is weight. The EV industry is tackling this challenge by reducing the weight and volume of the battery pack itself. Another option is to reduce the mass of the heat sink, which also takes up a considerable amount of volume and weight.
One of the optimization goals that Diabatix can optimally design for is mass reduction. Through the thousands of design iterations that our artificial intelligence creates, the result is a lightweight and thin design that retains its high thermal efficiency. Diabatix has achieved mass reductions of up to 40%, as can be viewed in the design comparison below.
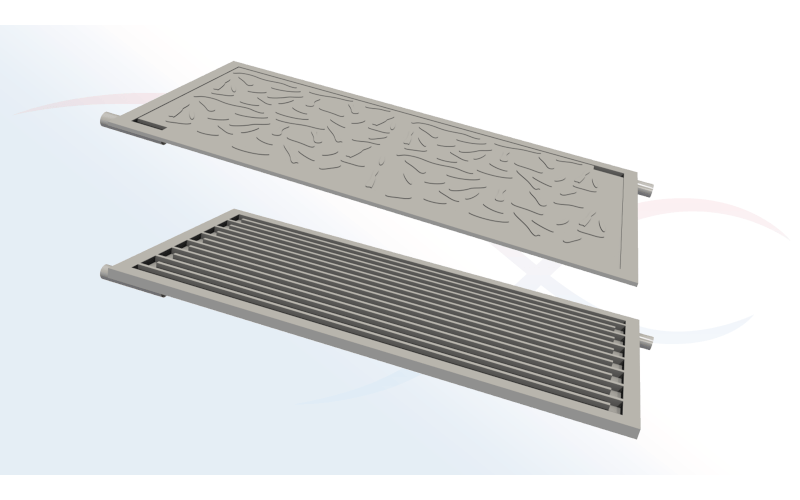
Reducing mass in a heat sink has the added advantage that less material is needed for production. It is therefore not only lighter, but also cheaper.
“With our AI driven generative thermal design approach, we are bringing high thermal efficiency, low weight, and a fast design process to the table for the EV industry. We are prepared to cool the e-motors and batteries of EVs not only today, but also those of tomorrow”, says Vervecken.
Follow us on LinkedIn for our latest news.
Discover Related Articles
- Building a Secure Engineering SAAS Platform
- Diabatix Gen-AI Technology Generates World’s Most Powerful Heatsink for Extreme CPU Cooling
- Integrating Additive Manufacturing with Design Automation
- Integrating Thermal Management From the Start
- Optimizing Cold Plate Performance Through Generative Design
- Passive Cooling vs. Active Cooling
- Revolutionizing Thermal Management: Diabatix's Solutions
- There’s a Right Coldstream License for Everyone
- Thermal Analysis for LED & Light Industry
- Thermal Management of EV Batteries Cold Plates
- What is Additive Manufacturing: A Comprehensive Guide for Engineers