Battery cold plate design is a critical aspect of electric vehicles (EVs) to ensure efficient thermal management and prolong battery lifespan. Conventional design methods often rely on human expertise and trial-and-error approaches. However, generative design with topology optimization (TO) offers a more effective and automated solution.
Conventional Cold Plate Designs
Conventional cold plate designs have been widely used in the industry to cool EV batteries. However, these designs often require human intervention and iterative processes.
We chose two different types of conventional designs: s-shaped and dimpled designs, to compare them with a generative-designed cold plate under the same conditions.
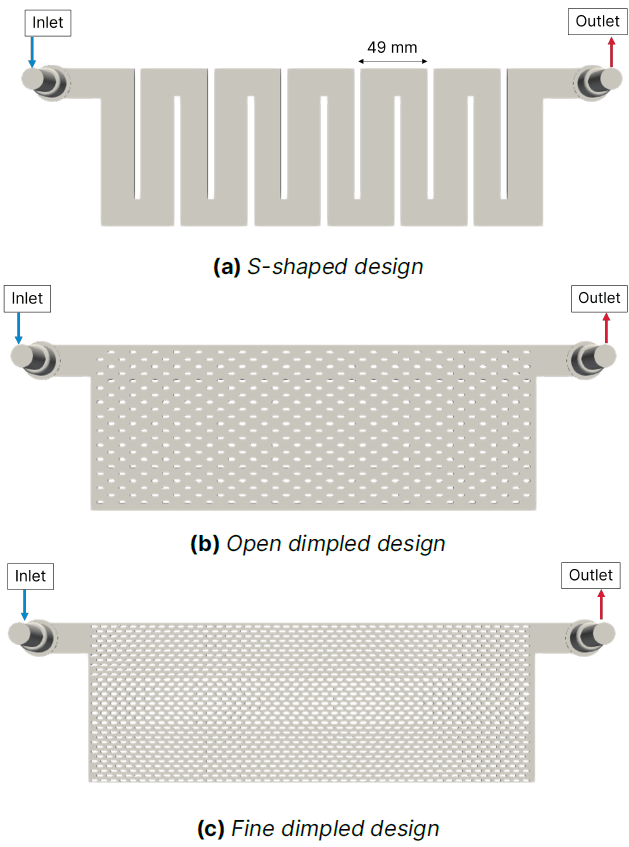
Topology Optimization for Battery Cold Plates
TO is a powerful technique that aims to find the optimal material distribution within a given design space. By integrating fluid mechanics and design constraints, it can generate highly performant cold plate designs. This approach considers factors such as temperature distribution, pressure drop, and manufacturability.
Ready for In-depth Info? Grab the White Paper Now!
Design Process
The design process involves several steps - automatically performed by ColdStream:
- Design Evaluation: Fluid flow and temperature distributions are evaluated using Computational Fluid Dynamics (CFD) simulations. This provides insights into the velocity, pressure, and temperature fields of the fluid and solid domains.
- Performance Evaluation: The numerical solution obtained from the CFD simulation is used to evaluate the design's performance against optimization targets. If the performance meets the targets, the optimization process ends, and the design is exported. Otherwise, the optimization loop continues.
- Sensitivity Analysis: Sensitivity analysis helps determine how the design should change to improve performance. The adjoint approach calculates sensitivities, allowing for efficient analysis of design variations.
- Design Update: Based on the current design and sensitivity analysis, the optimization algorithm proposes a new design. This serves as the starting point for the next iteration of the optimization process.
After the iterative process, the generative-designed cold plate is ready:
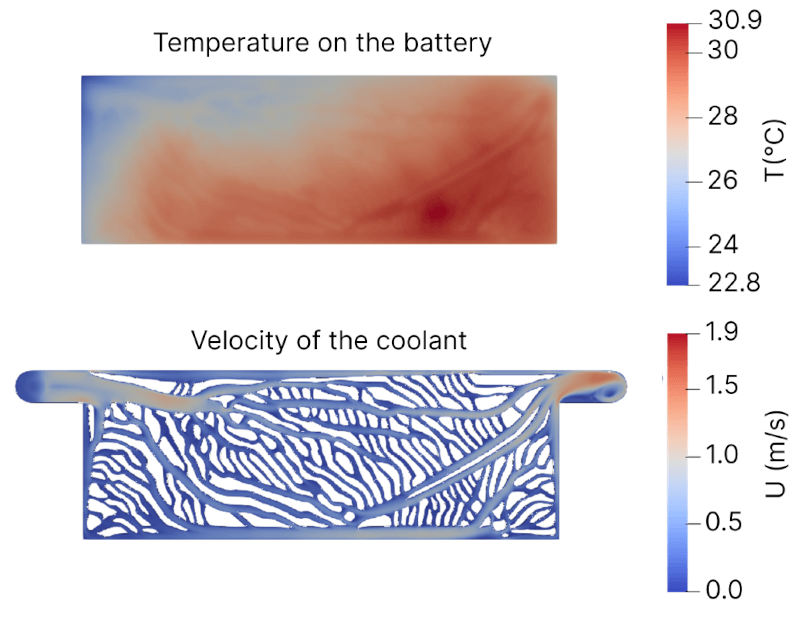
See the Breakdown: Access Our Complete Case Results Here!
Generative vs. Conventional Design – Who Leads the Way?
The performance of different designs, including S-shaped, dimpled, and generative designs, is evaluated. The conventional designs can operate as desired, either for peak temperature, temperature uniformity, or pressure drop. However, they do not fulfill all the scenarios simultaneously, as with the custom design. With the overview of the results, it is clear the cold plate generative design has an ultimate performance.
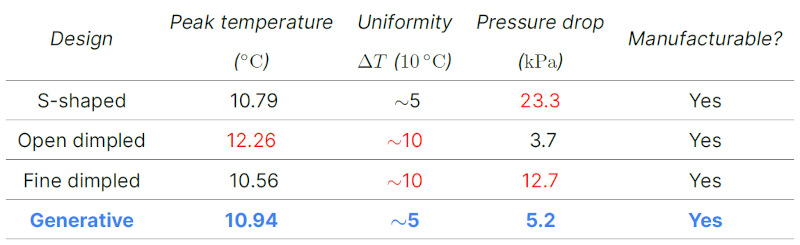
Conclusion
Generative design offers a promising solution for battery cold plate design in EVs. By automating the design process and considering various constraints, this approach can generate highly efficient and performant designs. Integrating fluid mechanics and sensitivity analysis provides valuable insights for optimizing battery thermal management.
Get in Touch!
‍