Automated design processes and Additive Manufacturing (AM) have significantly changed the manufacturing industry. The integration of these two powerful technologies is reshaping the way products are designed and produced. With automation and 3D printing capabilities, manufacturers can now create complex and intricate designs with incredible speed, precision, and efficiency. This combination is leading the charge toward a more sustainable, accessible, and affordable future for manufacturing.
Beyond its versatility, AM stands as a symbol of sustainable manufacturing practices. It signifies a departure from the waste-intensive methods of the past by using only the necessary materials to build a part, thus significantly reducing the carbon footprint. As businesses become more environmentally conscious, AM becomes an increasingly attractive option, marrying economic benefits with ecological responsibility.
Understanding Additive Manufacturing
Additive Manufacturing is often synonymous with 3D printing, but it includes more than just that. This field involves constructing objects layer by layer, enabling the creation of structures that would challenge conventional manufacturing methods. The inherent flexibility of AM allows for an expansive range of applications, from intricate components in aerospace to bespoke fashion pieces.
Learn more about 3D printed heat sinks here
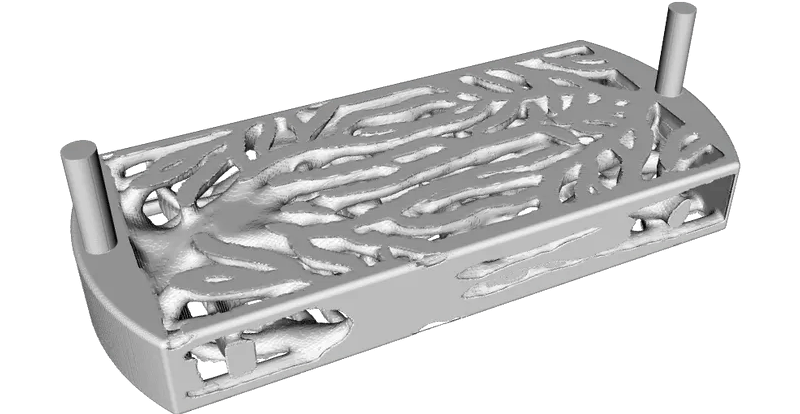
In addition to its versatility, AM is also an excellent example of sustainable manufacturing practices. It is an eco-friendly alternative to traditional manufacturing methods as it only uses the necessary materials to build a part, resulting in a significant reduction in environmental waste - in some cases, as much as 90% compared to conventional manufacturing [1]. As a result, businesses are increasingly adopting AM as a responsible and cost-effective manufacturing option, aligning with their environmental goals.
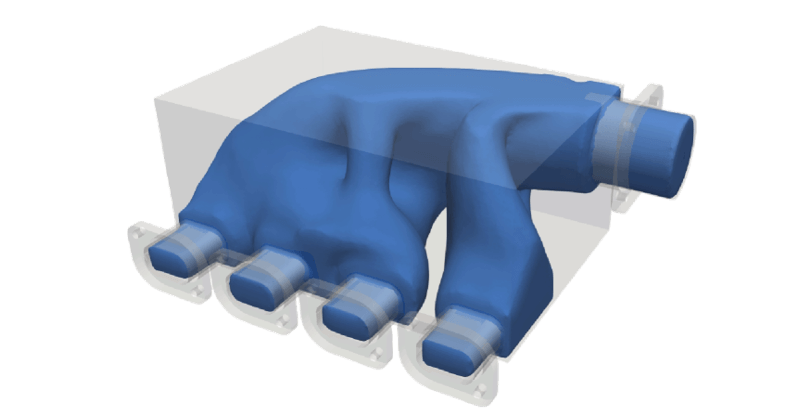
Automated AM in Thermal Design
Automated thermal design is changing how engineers approach temperature management in electronic devices, machinery, or batteries, where precision is essential. Diabatix's software, ColdStream, represents this advancement by utilizing generative AI to automate the design of cooling solutions.
ColdStream incorporates cutting-edge generative design technology to calculate and iterate designs autonomously, optimizing for the most effective heat dissipation pathways. By automating work iterations, engineers can save significant time and ensure that the designs are efficient and manufacturable. This automated process not only speeds up the design phase but also achieves a level of optimization beyond what can be achieved through manual calculations.
ColdStream's role extends to the field of predictive analysis, predicting thermal performance before a prototype is ever constructed. Engineers can ensure that the final product operates within desired temperature ranges by simulating real-world conditions and providing precise thermal assessments. This foresight is crucial in industries where thermal efficiency translates to reliability and longevity, such as aerospace, automotive, and high-performance computing.
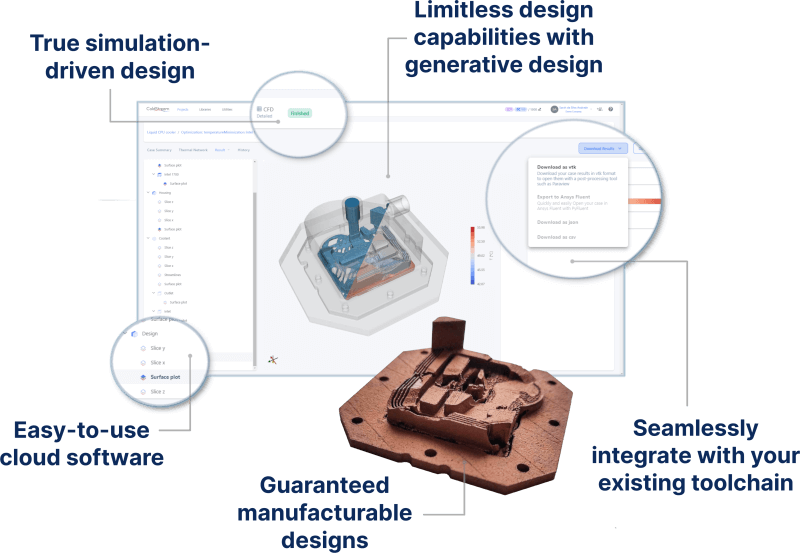
A Synergistic Relationship
The combination of automated design and AM is product development. ColdStream can directly take into account AM manufacturing specifications, sending complex designs straight to production without the need for intermediary steps. This streamlined workflow results in a significant reduction in lead times and provides a level of agility that is invaluable in today’s fast-paced market.
.jpeg)
Additionally, this union creates fresh opportunities for personalization. As consumer demand continues to shift towards personalized products, the combination of automated design and AM is expected to be a key factor in the thermal management industry. By integrating AM into the production process, companies can create personalized products with a reduction of 80% in engineering time and 20% more cooling performance.
Use Case: Double-Sided Power Inverter
But how does it work in practice? Let's examine the cooling system design of a double-sided power inverter.
The cooling system should regulate the temperature of chips, generating a heating power of Q = 4002W, which is spread by copper heat spreaders. The fluid is a mixture of water and glycol in a ratio of 40/60.
ColdStream considers manufacturing a constraint that should be selected before optimization. The cooling system for the power inverter was designed to be produced using 3D printing technology. After setting up the design area and optimization targets of temperature minimization, temperature variance minimization and manufacturing, ColdStream handles the cooling component optimization autonomously.
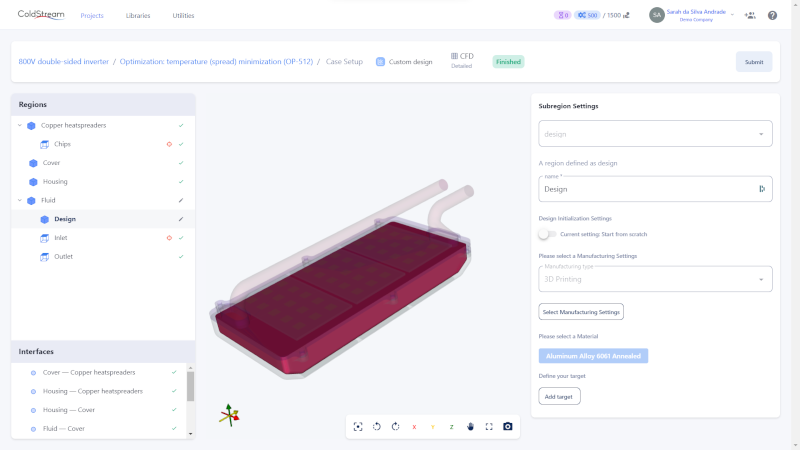
Discover the 3D-printed cooling design that is ready to be manufactured by visiting the 3D results tab:
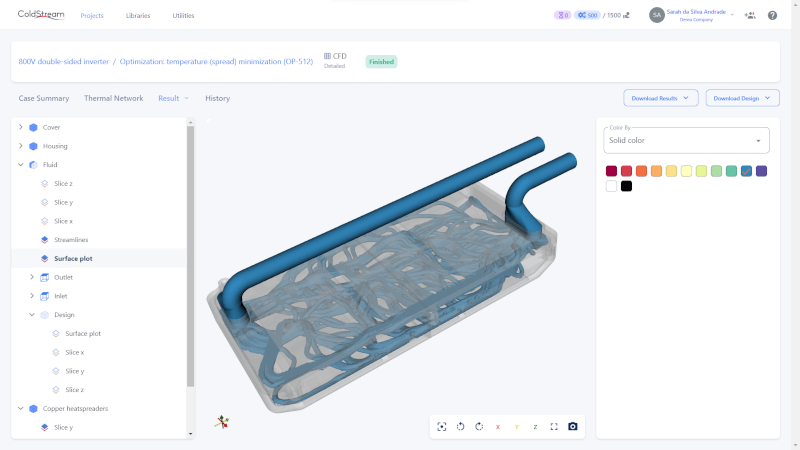
ColdStream platform enables visualization of complete results, including 3D representations, tables, and charts. Moreover, you can download the results and integrate them into your toolchain's workflow for better performance.
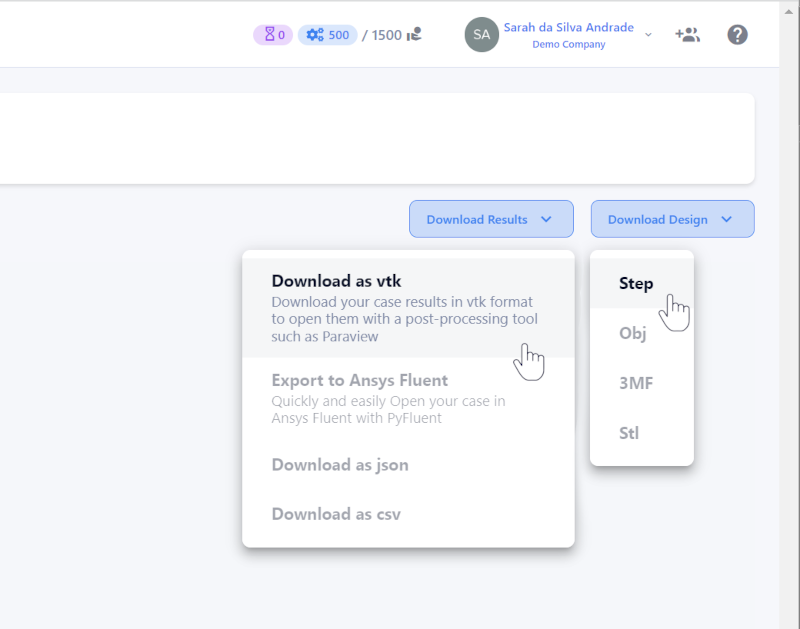
Envisioning the Future
Thermal automated design and AM are coming together, promising to bring a revolution in manufacturing. This new era will be characterized by the ability to cater to individual needs and preferences. With the help of this technology pairing, we can expect traditional manufacturing to be disrupted, and producing customized and complex products at a fraction of the current cost and time will become a reality in the future.
Diabatix's ColdStream software complements additive manufacturing hardware investment, offering design flexibility at various resolutions. By utilizing generative design and advanced algorithms, Diabatix achieves highly detailed and precise parts. ColdStream optimizes cooling systems with thermal analysis, reducing distortion and improving part fit. If you are facing any of these challenges, reach out to Diabatix to unlock the full potential of additive manufacturing and achieve a rapid return on your AM investments.