The demand for automotive lithium-ion (Li-ion) batteries has increased significantly to 550 GWh in 2022, which is a 65% rise from 330 GWh in 2021 [1]. This phenomenon is mainly due to the high demand for electric vehicles (EVs). It is forecasted that the global market for EVs will reach $906.7 billion by 2028, up from $538.8 billion in 2022 [2]. These numbers depict the rapid growth of the electric vehicle industry and its potential to drive innovation in EV-related technologies.
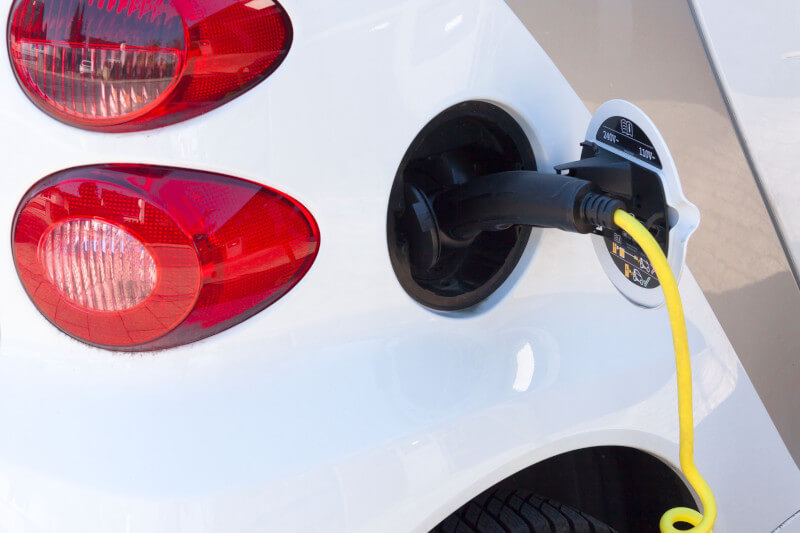
As the heart of EVs, batteries not only need to store large amounts of energy but also require efficient cooling mechanisms to maintain optimal performance and ensure longevity. Therefore, the automotive industry is intensifying its focus on developing advanced cooling solutions, which has led to increased demands for more sophisticated and automated design processes.
The Importance of Advanced Cooling in EVs
The battery pack is a crucial component of an EV as it ensures energy storage and power supply. To keep them operating within their ideal temperature range, it is essential to maintain optimal temperature ranges. Advanced cooling solutions are therefore necessary to prevent thermal degradation, prolong battery life, and avoid dangerous situations such as thermal runaways.
Managing temperature levels in EV batteries is a complex process that poses various challenges. While efficient heat dissipation is a key consideration, it must also be energy-efficient, space-saving, and cost-effective. Air cooling methods are often insufficient for modern EV batteries, and more advanced techniques like liquid cooling systems are now commonly adopted due to their superior heat transfer and precise control. However, integrating these cooling systems into EV designs requires careful consideration of additional factors such as weight and space constraints, ensuring that they do not impact the vehicle's range and performance negatively.
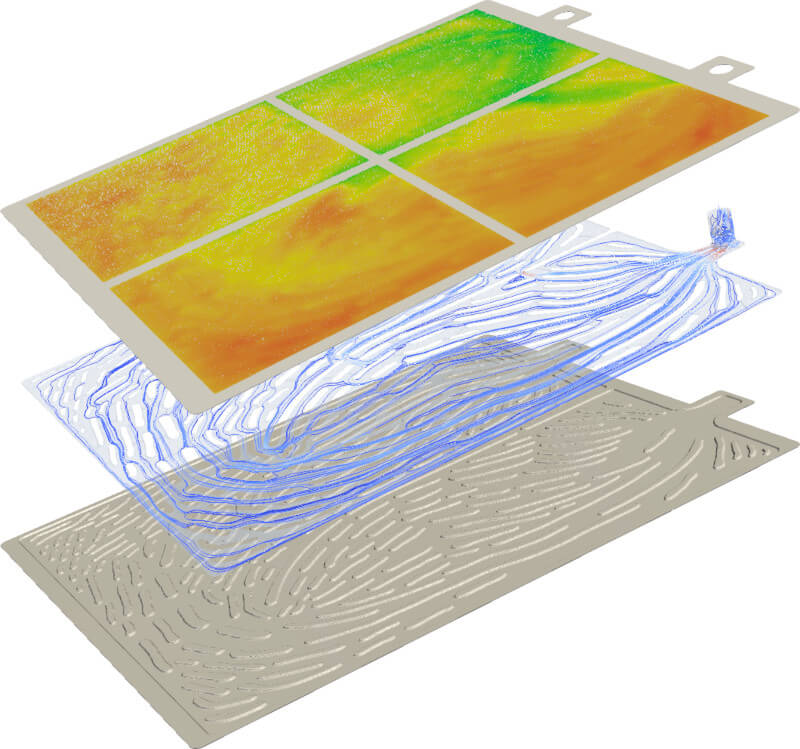
Developing EV cooling systems requires meeting technical requirements while also considering environmental factors. Since EVs are considered a sustainable alternative to traditional vehicles, all components, including cooling systems, must align with environmental goals. Eco-friendly refrigerants, reducing energy consumption, and assessing the overall lifecycle impact of cooling components are some of the ways to achieve this. Therefore, the success of the EV industry relies not only on the batteries themselves but also on the effectiveness of the cooling solutions that maintain their optimal operation.
Leveraging Generative Design
ColdStream is a key player in innovating EV cooling systems, with a focus on designing cooling plates. Diabatix’s thermal generative design software significantly streamlines and accelerates the design process. Engineers input operational parameters and constraints ColdStream, which then uses these guidelines to iteratively generate concepts and optimize designs. The primary objective of this process is to optimize critical factors such as thermal uniformity and heat exchange efficiency, ensuring that the designs not only meet the required performance standards but also align with the operational realities of EV cooling systems.
Try ColdStream
The strength of ColdStream lies in its versatility and adaptability. It is capable of handling a range of cooling scenarios and accommodating different manufacturing constraints, which is especially pertinent given the complexities of advanced sheet metal forming processes used in EV manufacturing. This adaptability is essential for tailoring cooling solutions to the specific needs of each vehicle, ensuring that the cooling systems are not only efficient and effective but also feasible to produce. By integrating these various aspects of design and manufacturing, Diabatix’s thermal generative design software emerges as a vital tool in the development of advanced cooling technologies for the rapidly growing EV industry.
Case Study: Optimizing Battery Cold Plates
A practical application of the thermal generative design is demonstrated through a case study on a sheet metal battery cold plate. The case study illustrates how ColdStream aligns design optimization with the unique aspects of the sheet metal forming technique. The result is a high-performing design that eliminates manual errors and streamlines the design process.
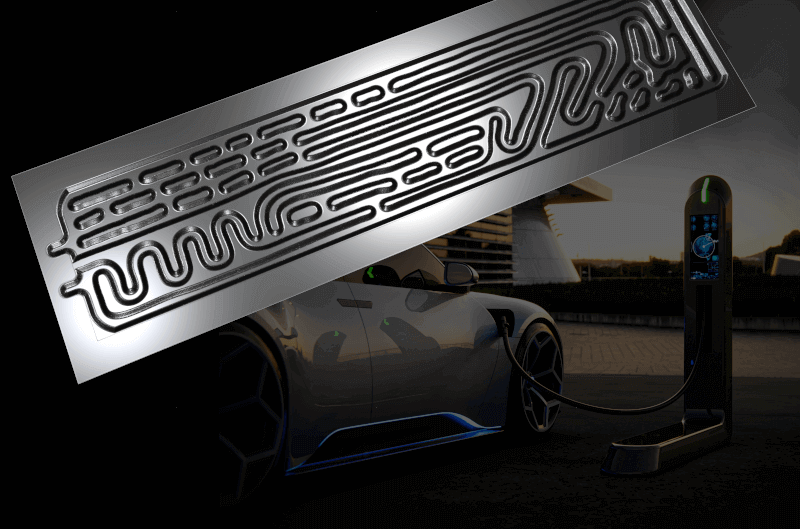
Check the full case study
The Future of EV Cooling Technologies
The collaboration between advanced manufacturing processes and thermal generative design software has reached a significant milestone in electric vehicle (EV) technology. These innovations highlight the importance of efficient cooling solutions in improving the performance and safety of EVs. As the market continues to expand, advanced technologies like these become increasingly critical. They offer not only better thermal management solutions but also pave the way for more sustainable and energy-efficient manufacturing practices.
‍
References
[1] https://www.iea.org/reports/global-ev-outlook-2023/trends-in-batteries
[2] https://www.statista.com/statistics/271537/worldwide-revenue-from-electric-vehicles-since-2010/