The world of manufacturing has undergone a seismic shift in recent decades, largely driven by the rise of additive manufacturing (AM). This revolutionary technology, often referred to as 3D printing, is reshaping industries across the board. It's time to delve deeper into the process, history, challenges, and advantages of AM as well as its future potential.
The concept of Additive Manufacturing can be traced back to the 1980s when Dr. Hideo Kodama, a Japanese researcher, developed an early version of a 3D printing process called "stereolithography." Around the same time, American engineer Charles Hull invented the "stereolithography apparatus" (SLA) and co-founded 3D Systems Corporation, which played a pivotal role in popularizing the technology.
However, it was not until the early 2000s that 3D printing made significant strides in terms of capabilities and accessibility. Advancements in materials, printing technologies, and affordability led to a broader range of applications beyond its initial use in prototyping. Industries such as aerospace, automotive, healthcare, and consumer goods started to explore the potential of additive manufacturing.
But what is it, and why is it considered a game-changing manufacturing technique?
1. The Basics: Defining Additive Manufacturing
Additive manufacturing, at its core, is the process of creating an object by building it one layer at a time. This is fundamentally different from traditional manufacturing, which relies on subtractive methods, cutting away material from a solid block to achieve the desired shape.
To put it simply, AM is about addition, not subtraction. It involves adding material, layer by layer, based on a digital model, which serves as a blueprint for the physical object. This method stands in stark contrast to conventional manufacturing, which generates significant waste by removing material.
The scope of AM is broad, ranging from creating intricate prototypes to crafting functional, end-use products. Over time, AM has evolved from its early days of non-functional prototypes into a game-changing technology used by industry giants like Boeing and General Electric.
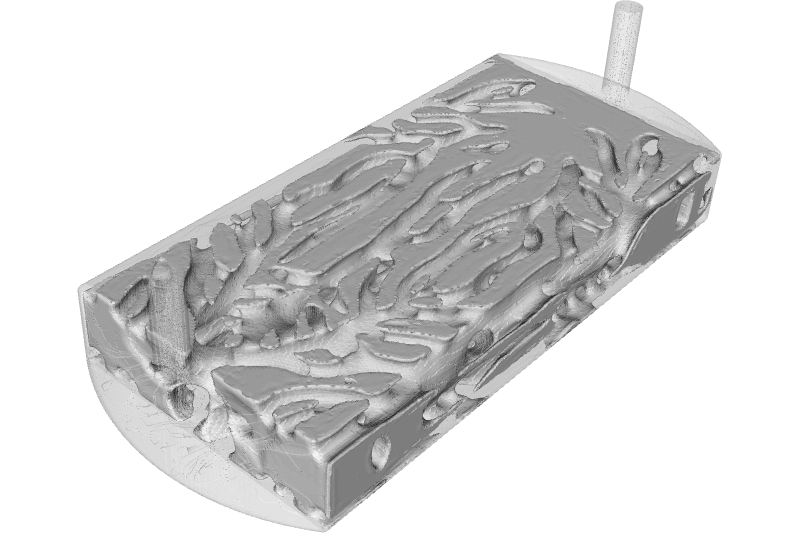
2. The Technology Behind AM
The process begins with the creation of a 3D model using Computer-Aided Design (CAD) software. This digital model serves as the starting point for the object that will be brought into the physical world through 3D printing. The digital model is then meticulously sliced into thin horizontal layers, and it's here that the magic of AM truly begins.
Each layer of the digital model is meticulously translated into a layer-by-layer framework for the AM machine to follow. This process is akin to instructing the machine to build the object, one layer at a time. The range of materials available for AM is extensive, covering polymers, metals, ceramics, foams, gels, and even biomaterials.
This versatility in material selection is a hallmark of AM and is a significant factor behind its broad applicability. AM technology continues to advance, with an expanding range of materials and printing technologies, pushing the boundaries of what is achievable in terms of precision, speed, and material diversity.
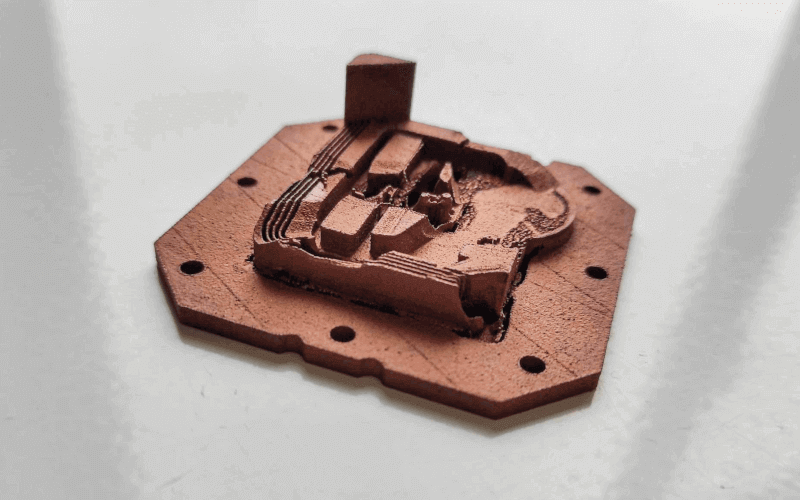
Various techniques fall under the umbrella of AM, each with its unique approach and advantages:
- Fused Deposition Modeling (FDM): In this technique, a thermoplastic filament is melted and extruded through a nozzle, building objects layer by layer. It's known for its utility in rapid prototyping and creating functional parts.
- Stereolithography (SLA): SLA uses a laser to cure and harden a liquid resin, layer by layer. This method is renowned for its precision and is often used in applications requiring intricate details.
- Selective Laser Sintering (SLS): SLS employs a laser to fuse powdered material layers. This method is particularly suitable for producing parts with complex geometries and can utilize various materials, including plastics and metals.
- Metal 3D Printing: Similar to SLS, metal 3D printing utilizes metal powders. It is a game-changer for industries where high-strength metal components are required, such as aerospace and automotive.
- Binder Jetting: In this process, a liquid binding agent is deposited to bond powder particles. It's advantageous for creating prototypes and functional parts focusing on cost-effectiveness.
These are just a few of the many methods available, and new innovations and techniques continue to emerge regularly, expanding the realm of possibilities for engineers and designers.
3. Benefits of Additive Manufacturing
One of the most remarkable aspects of additive manufacturing is its ability to reduce waste and enhance sustainability. Traditional subtractive manufacturing methods often result in a significant amount of material wastage, which involves removing material from a larger block to create the desired part. This not only increases the cost of production but also contributes to the environmental footprint.
In contrast, additive manufacturing only uses the necessary material, reducing environmental impact and material costs. Moreover, AM allows for on-demand production, reducing the need for extensive storage and transportation of pre-fabricated parts. This shift towards localized, on-demand production holds the potential to reshape supply chains and manufacturing processes, leading to more efficient and sustainable methods.
AM represents not just a technological advancement but a force that is ready to reshape industries and redefine how we think about manufacturing in the 21st century.
Summarizing the benefits of AM:
- Complex Geometries: AM can produce complex structures that are impossible with traditional methods. This capability is especially advantageous in aerospace, where lightweight and intricately designed parts can enhance fuel efficiency and overall performance.
- Rapid Prototyping: With 3D printing, the journey from design to prototype is drastically shortened. This speed is invaluable in industries where time-to-market is a critical factor.
- Customization: Additive manufacturing is ideal for creating personalized products or medical implants tailored to individual needs. Healthcare is a prime example of an industry benefiting from personalized 3D-printed solutions.
- Reduced Waste: Unlike traditional methods, AM only uses the necessary material, minimizing waste. This reduction in material waste is a significant environmental advantage.
- Supply Chain Simplification: Direct production through additive manufacturing can reduce the need for extensive inventory and multiple manufacturing steps. This simplification can lead to cost savings and improved efficiency.
4. The Role of Diabatix in AM
Diabatix, a specialist in generative thermal design, offers solutions to address some of the most common challenges associated with additive manufacturing:
a) Generative Design for Precision: Diabatix software, ColdStream, employs advanced algorithms for generative design. This enables the creation of highly detailed and accurate part geometries even with FDM (Fused Deposition Modeling) printing. With this approach, additive manufacturing can reach a level of precision that rivals traditional manufacturing methods. It's a game-changer for engineers and designers who seek intricate, precise parts.
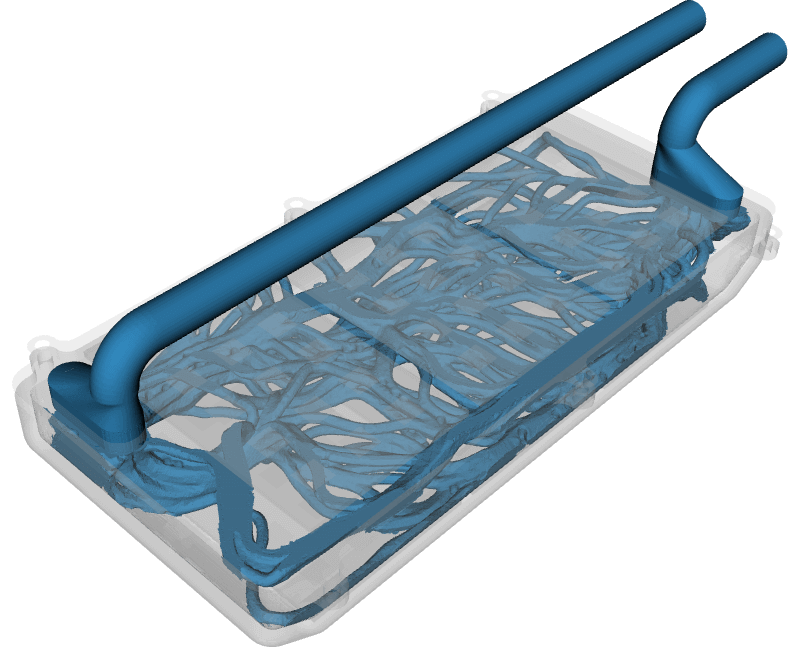
b) Thermal Analysis for Improved Quality: Advanced thermal analysis software is utilized to optimize the design of cooling systems and mitigate warping and shrinkage issues during printing. By considering thermal properties during the design phase, ColdStream creates parts that are less susceptible to distortion, ensuring a better fit and function. This aspect is particularly crucial in industries where precision and quality are non-negotiable.
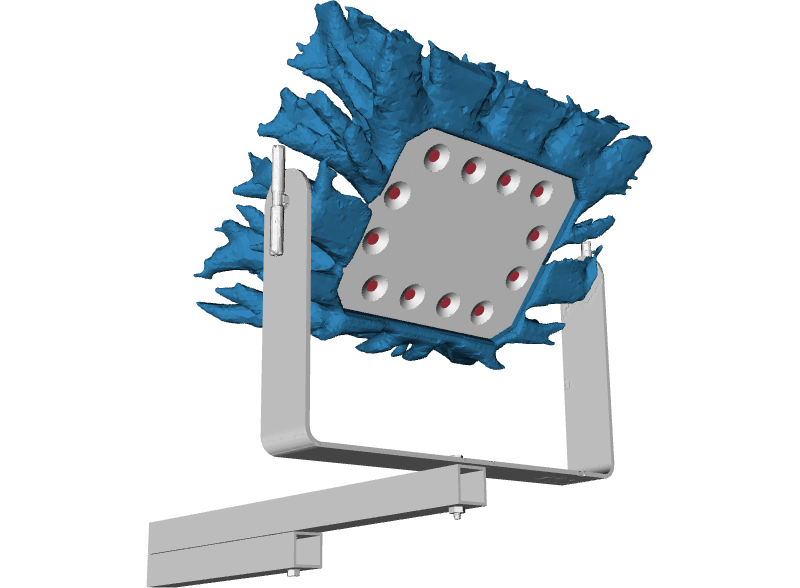
c) Material Freedom: Users can directly input proprietary materials into the AM process. This feature enhances the quality and consistency of printed parts. Laser-absorptive and oxidation-resistant powders, for instance, can improve flowability and reduce oxygen in the final part, ultimately enhancing strength and durability.
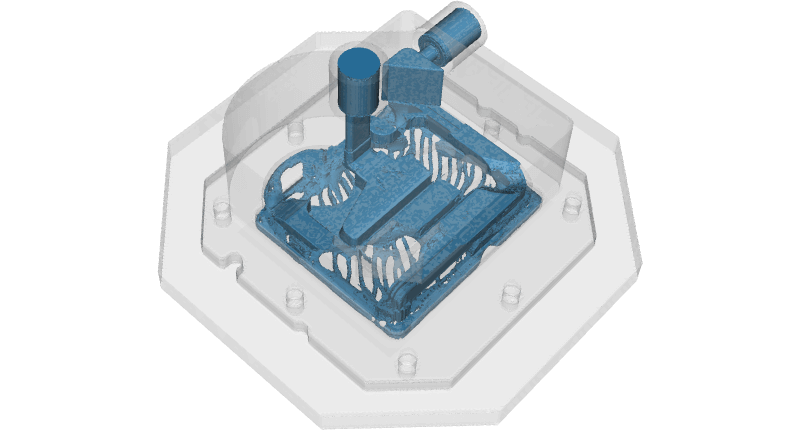
By combining AI algorithms, thermal analysis capabilities, and material freedom, ColdStream enables engineers and designers to achieve precision, accuracy, and durability in 3D-printed components on par with traditional manufacturing standards. This is a significant step towards making additive manufacturing the go-to choice for complex, high-precision parts.
5. Additive Manufacturing: What's on the Horizon?
In the world of 3D printing, the future is already here, and it's set to reshape how we think about design and manufacturing. As 3D printing technology becomes more accessible and user-friendly, designers will have greater creative freedom. AI-driven tools will assist in creating optimized designs, making complex geometries and efficient structures achievable with ease. In fact, ColdStream, by Diabatix, is one such tool that's available today to assist engineers in optimizing their designs.
With materials being a crucial component of 3D printing, we can expect to see continual improvement in material properties. Materials will become stronger, more durable, and longer-lasting. Furthermore, the ability to print components with multiple materials will open the door to smart materials with built-in sensors and electronics. This development is particularly exciting for industries like healthcare, where the integration of sensors into 3D-printed medical devices can revolutionize patient care.
Lastly, 3D printing offers a sustainable approach by significantly reducing waste generation. As it spreads across sectors, we can anticipate a rising demand for tailor-made products, be it in aerospace, healthcare, or consumer goods. However, with this expansion comes the imperative need to implement rigorous regulations to ensure safety and maintain high standards of quality. The evolution of 3D printing will revolutionize material selection and manufacturing processes across diverse industries.
Conclusion
Traditional manufacturing methods, including subtractive techniques and molding processes, have been the backbone of the production industry for many years. However, these methods come with inherent drawbacks.
Firstly, subtractive techniques often lead to material wastage since they involve removing materials from a larger block to create the desired part. This not only increases the cost of production but also the environmental footprint. Mold-based processes, on the other hand, demand significant upfront investments in creating molds, making them cost-inefficient for low-volume or customized productions. Furthermore, traditional methods can restrict design freedom, complicating the production of intricate geometries and internal structures.
Explore ColdStream
The future of manufacturing is being redefined by the rapid advancements in AM. This technology builds objects layer by layer, adding material only where it's needed, which significantly reduces waste. The beauty of AM lies in its ability to produce complex and customized parts without the need for specialized molds or tooling. This not only democratizes design and production, making it accessible for small businesses and individuals but also paves the way for innovations in various sectors. As the technology matures, its cost-effectiveness, speed, and material diversity are expected to improve, heralding a new era where additive manufacturing might well become the default choice for a vast range of applications. The journey of additive manufacturing is not just about its present capabilities but its boundless potential to reshape industries and make manufacturing more sustainable, efficient, and innovative.