Designing an efficient cooling system is certainly challenging. The decision-making path can be overwhelming since several variables are influencing the cooling mechanism. To help you with this process, we will explore in this article the three most important choices to make when designing your cooling system:
- What coolant to use?
- What is the driving force causing the fluid motion?
- How is the cooling system manufactured?
The answer to these three questions will have a big impact on what your cooling solution will look like and how it will perform.
1. What coolant to use for the cooling system?
Despite water being the most obvious choice as it is abundantly available, its high conductivity makes it a less than ideal option for electronic applications. Adding anti-freezing agents (like glycol) to water will solve the issue, turning it applicable to cool down electronic components. Clearly, modifying the relative volumetric fraction of water and glycol will change the material properties of the mixture.
All materials have properties that depend on the local temperature. Taking this into account will increase the computational time required to simulate the system. When the temperature difference in your components is not significant, it does not warrant temperature-dependent material properties as the relative error falls within the margin of error that can be expected from numerical simulations.
ColdStream has an extensive material library into which its users can store material properties. The library already contains several predefined materials, however, the platform has also a feature where its users can add their custom materials to the library. The material properties input can be either temperature dependent or temperature independent based on the users’ preference. The following image showcases an example of how the density can evolve with the temperature.
.png)
2. What driving force causes the fluid motion?
Cooling systems can rely on two distinct driving forces for the coolant to circulate throughout the geometry.
- The first driving force is natural convection, where the heat up of the fluid causes the fluid to expand locally. This localized expansion causes the hot fluid particles to flow upwards and the colder fluid particles to sink.
- The other driving force is called forced convection, where a fan (for gaseous coolants) or a pump (for liquid coolants) converts an external energy source (typically electric energy) into kinetic energy. This driving force is the most commonly used one for cooling systems as it allows for the highest heat exchange rate.
Fans and pumps behave interestingly, given that their flow rate depends on the load of the system. This behavior is represented by the performance curve of the fan/pump. A typical performance curve has a negative evolution of the pressure with the flow rate, which is illustrated bellow:
.png)
The load of the system, on the other hand, has an increasing pressure vs flow rate curve. This is what is known as the load curve of the system. The point where both curves intersect determines the operating point of the fan/pump.
Diabatix provides several predefined performance curves available through the fans and pumps library on ColdStream. Again, the user has complete control of their library and can add their own performance curves which are only accessible through their accounts for confidentiality reasons.
3. How will the cooling system get manufactured?
Every coolings system produced is constrained by its manufacturing techniques and settings or the ones of its partners. They impact the optimized design, so this must be taken into account while setting up the design process.
ColdStream allows its users to constraint the optimization process by feeding in the desired manufacturing technique together with the relevant manufacturing settings. ColdStream can work with the following manufacturing techniques:
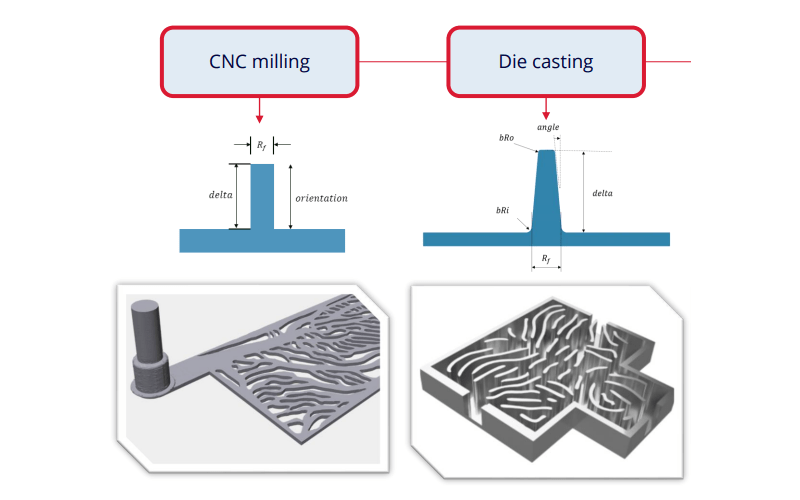
.png)
The two images below give a clear indication of how a CNC milled design differs from a 3D-printed design (for the same boundary conditions).
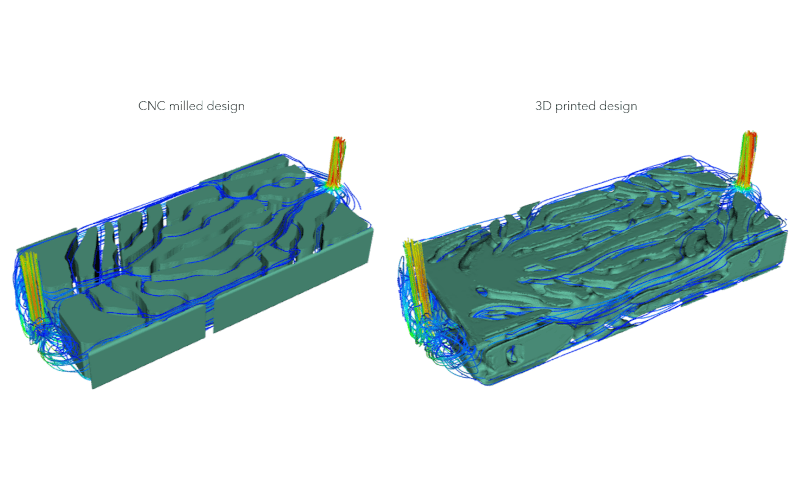
Conclusion
Before designing a cooling system, any engineer needs to thoroughly think about the three aforementioned questions and answer them: what coolant will cool down the heat-producing components and are temperature-dependent properties really needed?; what fan or pump will drive my flow, or will the cooling system solely rely on natural convection?; finally, how will the cooling system be made?
Answering these questions helps you define your problem and thus enables ColdStream to design the best cooling system for your application. For more information about how ColdStream can be tailored specifically to your needs, please contact our team and/or visit our documentation page.
Discover Related Articles
- 3 Design Methods to Future-proof Your Heat Sink
- 4 Optimization Targets for Cooling System Design
- Calculate Heat Sink Thermal Resistance Formula
- Generative Design Is Key to Heat Sink Innovation
‍
‍