Manufacturing techniques are crucial for cooling systems, impacting their efficiency, precision, and durability. Advanced methods ensure high-quality material use, accurate component construction, and improved thermal management, leading to more reliable and energy-efficient systems.
The three main techniques that we will discuss in this article are 3D printing, die casting, and CNC milling. Each technique has its strengths and limitations, and understanding them is essential to make informed decisions about the most suitable manufacturing technique for a specific application.
In addition to examining various manufacturing techniques, we will also investigate their effect on the optimal cooling solution for a power inverter. We will discuss the advantages and disadvantages of each technique and how it can be utilized in a specific application, such as a double-sided power inverter.
Manufacturing Techniques
Manufacturing techniques are crucial in determining optimal cooling solutions. This article discusses three techniques:
1. 3D Printing: Also known as additive manufacturing, this technique includes methods such as Selective Laser Sintering (SLS), Selective Laser Melting (SLM), and Laser Powder Bed Fusion (LPBF). 3D printing offers design flexibility and the ability to create complex, organic shapes. However, it may not be suitable for high-volume production due to its slow production speed and high cost.
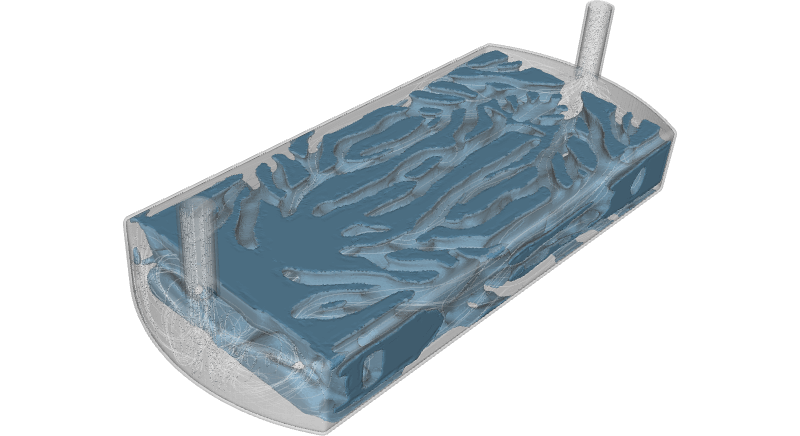
2. Die Casting: This manufacturing process involves pouring a liquid material into a mold, which then hardens into a solid. Die casting is a suitable method for producing large quantities of products and offers reasonable design flexibility within the limitations of the mold. Yet, it may not be ideal for complex shapes and may require additional machining.
.png)
3. CNC Milling: This subtractive manufacturing technique involves removing material from a solid block using a tool. CNC milling is suitable for lower volumes and prototyping, offering high design flexibility. It's worth noting that this method might not be the best choice if you're dealing with complex shapes and may require additional finishing.
.png)
Application: Double-Sided Power Inverter
A double-sided power inverter has two heat sources, located at the top and bottom respectively. The heatsink, which contains a fluid that transfers heat, is positioned between the two heat sources. The design domain, where optimization structures can be created, is located beneath the heat sources.
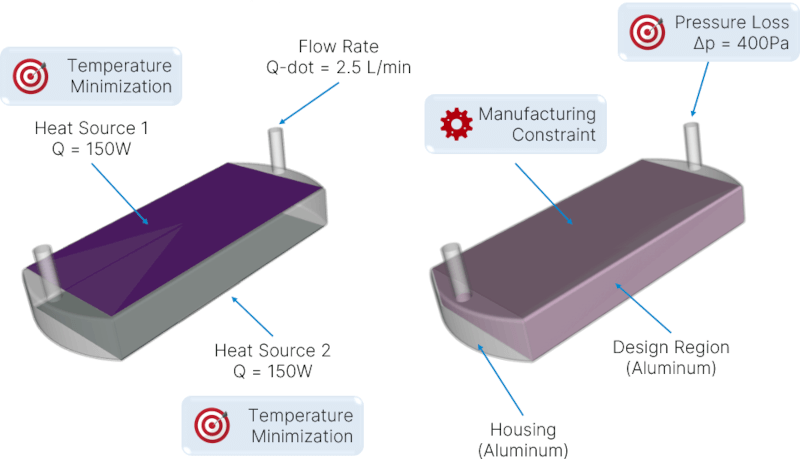
ColdStream Workflow
ColdStream is a generative design software that offers a streamlined design process to find optimal cooling solutions for any kind of cooling component. The workflow involves the following steps:
- Define Solids and Fluids: Specify the materials used (e.g., copper, aluminum, or plastic) and the fluid type (e.g., air-cooled or liquid-cooled).
- Define Boundary Conditions: Specify the heat load, type of convection cooling (natural or forced), and other relevant conditions.
- Define Design Domain and Targets: Set the design domain and select optimization targets, such as maximized heat exchange efficiency, concentrated pressure drop, or minimized weight.
Once the case is submitted, ColdStream will generate an optimized geometry in Stp file format.
.png)
Try ColdStream
Die Casting Example
Let’s check an example of using ColdStream to optimize the design of a double-sided power inverter using die casting for two different release angles. The design domain is 33 centimeters high, and the structures are made out of aluminum. The optimization targets are to minimize the temperature on both heat sources and to optimize for a given flow rate while keeping the pressure drop below 400 Pascal.
.png)
Check the full case study here
Conclusion
To make informed decisions about the most suitable manufacturing technique for your application, it is important to understand the strengths and limitations of 3D printing, die casting, and CNC milling. ColdStream software can help you streamline your design process by leveraging generative design to find optimal cooling solutions for cooling components. With the ability to optimize for multiple targets simultaneously, ColdStream can help you find the best possible solution for your specific application.