In the field of Computational Fluid Dynamics (CFD), getting accurate results depends heavily on several key factors. One of these factors is correctly matching the boundary conditions to reality. Simply put, boundary conditions help us define how a system interacts with its surroundings. Today, we're going to discuss boundary conditions, why they're important, and how to use them correctly in CFD simulations.
What are Boundary Conditions?
In the realm of CFD, boundary conditions are an integral part of the process. They must be specified to solve both ordinary and partial differential equations. These conditions can greatly affect your results, and poor choices may lead to solution divergence or even yield inaccurate solutions.
Boundary conditions often come in three forms:
- Dirichlet Boundary Conditions: Here, the value along the boundary is specified.
- Neumann Boundary Conditions: In this type, the value of the derivative is specified.
- Robin Boundary Conditions: Here, a combination of values and derivatives is imposed.
The Role of Boundary Conditions in CFD
In CFD software like Diabatix’s ColdStream, the Navier Stokes equations are solved, which require boundary conditions for the unknown variables. For instance, in three-dimensional momentum equations and the continuity equation, there are four unknowns (Ux, Uy, Uz and static pressure p); hence, four boundary conditions must be specified.
Navier-Stokes Equations:
- Continuity Equation
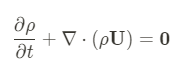
- Momentum Equation

Types of Boundary Conditions
There are various types of boundary conditions in fluid dynamics:
- Velocity Inlets: The velocity at which fluid enters the domain is known, and the pressure is calculated. This is often used when the flow rate is a known parameter.
- Pressure Inlets: The total pressure is specified, and the velocity is calculated. This type is typically used in buoyancy-driven flow problems.
- Fan/Pump Inlets: The static pressure is set based on the total pressure and the pressure drop, which is specified as a function of the volumetric flow rate across the patch.
- Pressure Outlets: The total pressure is specified, and the velocity is calculated.
- Wall Boundaries: Impermeable walls ensure no flow through them. At walls, a no-slip condition is applied, meaning the tangential velocity of the fluid at the wall is the same as the fluid velocity.
Applying Boundary Conditions: A Practical Example
Let’s consider an example of a cooling jacket case. The cooling jacket is an aluminum case placed over an electric motor. The motor isn't simulated; instead, it is simplified as a heated wall, one of the boundary conditions. The fluid region has an inlet and an outlet, indicating where the fluid enters and leaves the domain.
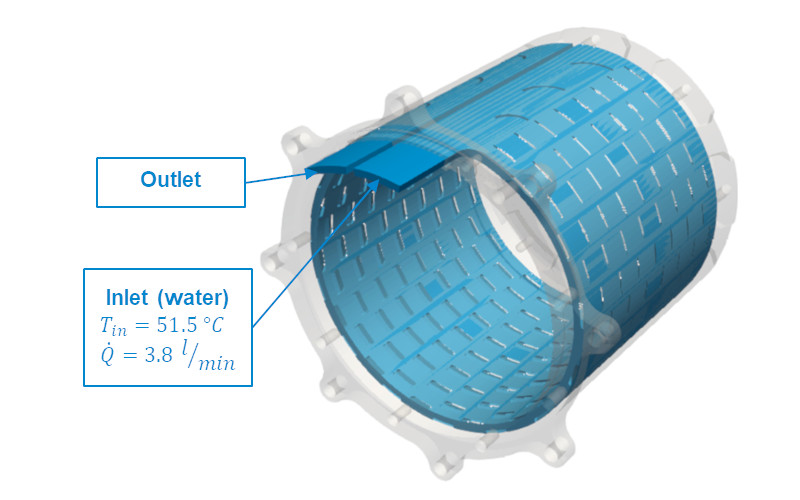
Using the ColdStream software, we can see and modify these conditions. By clicking on the fluid region, the inlet and outlet boundaries become visible. These boundaries can be created, replaced, or removed by clicking on the region and adding the boundary.
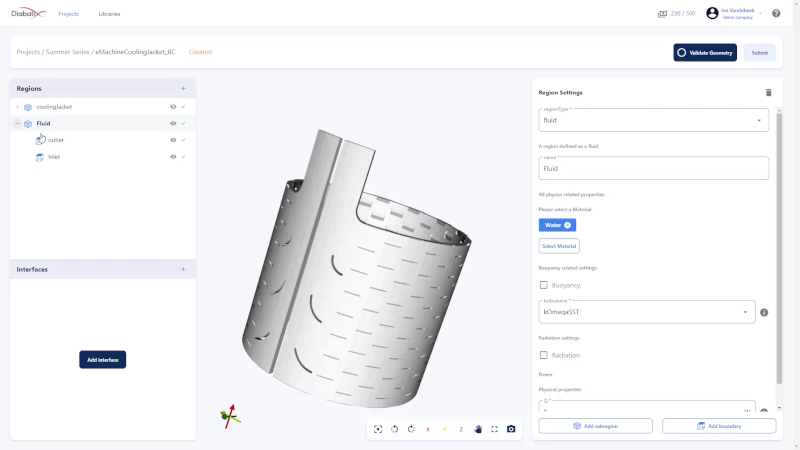
The wall boundaries can also be altered according to the simulation requirements. For instance, the motor can be simulated as a heated wall, applying a fixed heat flux boundary condition. Other options include: fixed temperature wall, which fixes the temperature of this wall to a constant value; external wall, which allows modeling the convective heat transfer to and from the environment; and insulated wall, which makes the boundary adiabatic.
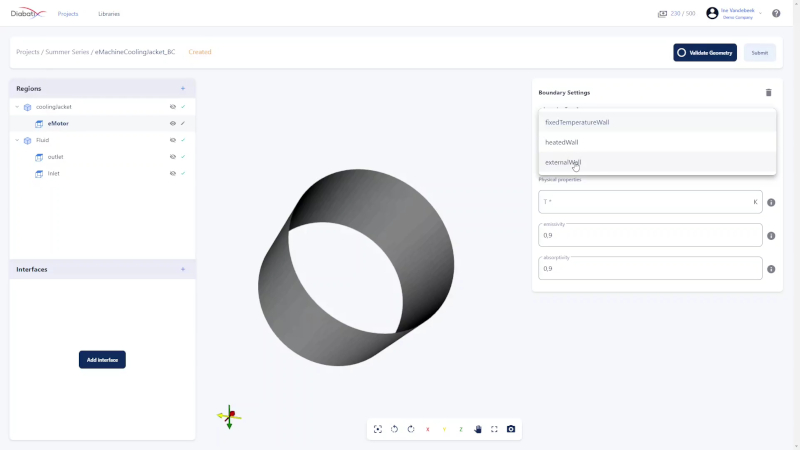
Try ColdStream
Concluding Remarks
Boundary conditions play a critical role in CFD simulations, affecting the accuracy and reliability of the results. They are an essential part of defining the problem and are necessary for obtaining a unique solution. Understanding these conditions and knowing when and how to apply them can enhance your simulation and make your CFD analysis more robust.
Have more questions? Feel free to reach out. We’re always here to help guide you on your CFD journey.
‍