Thermal network models are mathematical models which can be used to analyze and optimize flow and heat transfer in complex systems. They are based on the concept of breaking down a system into smaller, interconnected components, or "nodes," and representing the relationships between these components as equations that describe the flow, energy balance and heat transfer. Such models are used in various fields, including electronics cooling, automotive cooling systems, power electronics, and refrigeration systems.
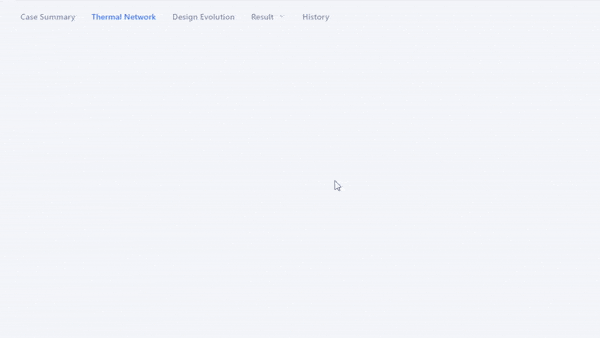
One advantage of thermal network models is their speed and accuracy. By reducing the system's complexity and focusing on energy balance and heat transfer, the number of variables that need to be solved is reduced, making the calculation more manageable and allowing for a fast solution. Additionally, thermal network models can study both steady-state and transient behavior, comprehensively understanding the system's performance.
Another advantage of thermal network models is their ability to provide a system-level solution, even when individual components are complex. This is particularly useful in the field of electronics cooling, where components such as power modules and inverters can be challenging to analyze. The thermal network model provides a high-level understanding of the system's behavior, making it possible to optimize the overall performance and efficiency.
However, a drawback of thermal network models is their reliance on correlations to estimate heat transfer between components. These correlations only exist for relatively simple geometries, meaning that accuracy may be limited for more complex systems. Additionally, thermal network models are a lumped approximation of the system. They may provide less detail than a computational fluid dynamics (CFD) model, which solves each system element's flow and heat transfer.
Compared to CFD models, thermal network models offer a faster and more manageable solution for system-level heat transfer analysis. However, CFD models provide more detailed information on flow and heat transfer and may be necessary for more complex systems. The choice between the two models depends on the applications' specific requirements and the trade-off between speed and accuracy.
In electronics cooling, thermal network models are frequently used to optimize system performance and efficiency. For example, a thermal network model may be used to analyze the thermal behavior of a power module, which converts electrical energy into heat. The model can be used to optimize the design of the power module, ensuring that heat is effectively transferred from the components to the cooling system, thereby improving performance and reliability.
Another example of the use of thermal network models in electronics cooling is in the analysis of an inverter, which converts direct current (DC) into alternating current (AC). In this case, a thermal network model can be used to understand the heat transfer between the components and the cooling system and to optimize the design of the inverter to ensure that heat is effectively dissipated.
Thermal network models are a valuable tool for thermal engineers, providing a fast solution for analyzing heat transfer in complex systems. They offer a system-level understanding of performance and efficiency and are particularly useful for optimizing the design of electronic cooling systems. Although the available correlations limit their heat transfer estimation accuracy and may provide less detail than a CFD model, thermal network models remain a powerful tool. The choice between thermal network models and CFD models will depend on the application's specific requirements and the trade-off between speed and accuracy.
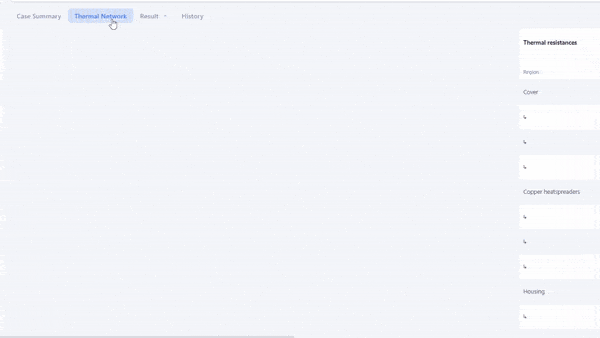
Best of all, thermal network models are available in ColdStream! When you submit a simulation case, you can click on "Submit as a correlation-based estimation" to get a thermal network analysis of your case. When you submit a standard design case, you can click "Submit as a correlation-based estimation" to get a thermal network-based parameter scan of the standard heat sink best suited to your setup. Alternatively, you can click on "Submit as a CFD reinforced estimation," in which case the thermal-network-based parameter scan is preceded by a CFD simulation for more accurate results. Thermal network-based results can be viewed in the "Thermal Network" tab next to the "Case Summary."
To know more about the thermal network on ColdStream, access our dedicated page or consult our documentation.