Introduction
As electronic devices become increasingly powerful and compact, effective thermal management has changed into a critical consideration for engineers. The efficient dissipation of heat generated by electronic components is essential for ensuring optimal performance, reliability, and longevity. In this guide to the thermal management of electronics, we will explore key principles, challenges, and strategies that engineers employ to tackle heat-related issues and design systems capable of withstanding demanding thermal conditions.
Understanding Thermal Challenges in Electronics
Electronics generate heat due to various factors, including power dissipation, switching losses, and electrical resistance. If not properly managed, excessive heat can lead to component degradation, performance degradation and premature failure. Therefore, engineers need to address the following thermal challenges:
Temperature Rise
Electronic components operating under high temperatures experience reduced efficiency, shortened lifespan, and increased risk of failures. Managing temperature rise is crucial to maintain performance and reliability.
Hotspots
Certain areas within electronic systems, such as processors, power modules, or integrated circuits, may generate significantly more heat than others. These hotspots demand focused attention to prevent localized overheating and ensure uniform temperature distribution.
.jpeg)
Thermal Cycling
Frequent temperature variations can cause thermal expansion and contraction of materials, leading to mechanical stress, solder joint fatigue, and potential failures. Thermal management must account for these thermal cycling effects.
Effective Thermal Management Strategies
To mitigate thermal challenges in electronics, engineers employ a variety of strategies and techniques:
Heat Sinks
Heat sinks are passive cooling solutions that enhance heat dissipation by increasing the surface area exposed to the surrounding air. They typically consist of fins or pins attached to heat-generating components and are often made of materials with high thermal conductivity, such as aluminum or copper. Heat sinks facilitate convective heat transfer, efficiently dissipating heat into the surrounding environment.
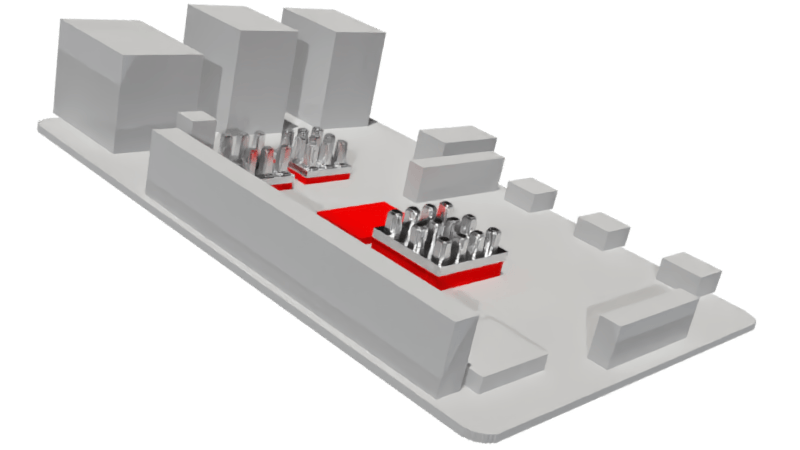
Thermal Interface Materials (TIMs)
TIMs are used to improve thermal conduction between electronic components and heat sinks. These materials, such as thermal greases, pads, or phase change materials, fill microscopic air gaps, enhancing heat transfer by reducing thermal resistance at the interface. TIMs ensure better thermal contact and promote efficient heat dissipation.
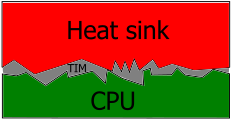
Airflow Management
Proper airflow within electronic systems is crucial for effective thermal management. Engineers design enclosures and use fans, blowers, or natural convection to ensure a continuous flow of cool air across heat-generating components. Optimizing airflow patterns, minimizing obstructions, and managing vent placements help dissipate heat efficiently and maintain lower operating temperatures.
Liquid Cooling
Liquid cooling systems offer enhanced heat dissipation for applications with high thermal demands. Liquid coolants, such as water or specialized fluids, flow through channels or heat pipes, absorbing heat from components and carrying it away. Liquid cooling is effective in scenarios where traditional air cooling methods are insufficient.
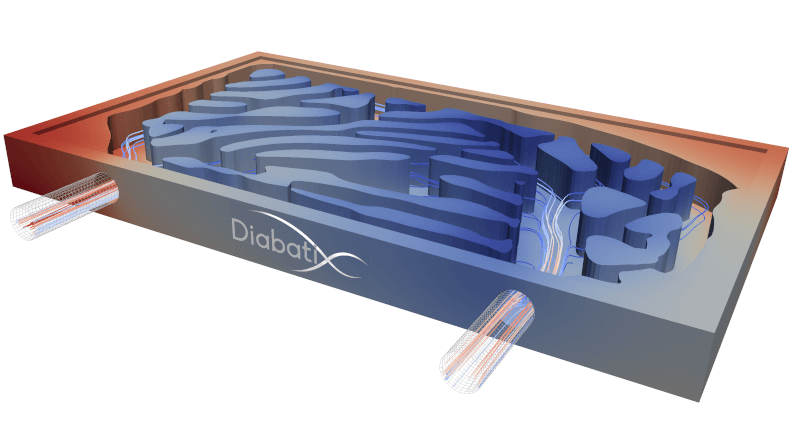
Thermal Simulation and Analysis
Engineers employ techniques such as computational fluid dynamics (CFD), an overarching term for solving fluid equations with a computer, and finite element analysis (FEA), one of the main methods to discretize the domain into cells, to simulate and analyze thermal behavior. These simulations aid in identifying hotspots, optimizing cooling strategies, and predicting temperature distributions within electronic systems, facilitating informed design decisions.
Conclusion
In the world of electronics, effective thermal management is crucial for maintaining optimal performance, reliability, and longevity. By understanding the thermal challenges faced by electronic components and employing appropriate strategies like heat sinks, thermal interface materials, airflow management, liquid cooling, and thermal simulation, engineers can design systems capable of enduring difficult challenges in thermal conditions. Implementing robust thermal management solutions ensures electronic devices operate within safe temperature ranges, reducing the risk of failures and maximizing their overall performance and lifespan.
‍