The domain of Computational Fluid Dynamics (CFD) and thermal simulations is one where precision holds the key. The quality of the input, Â specifically the mesh that defines the analyzed model's geometry, critically shapes the accuracy of the simulation outcomes. This mesh serves as a fundamental basis for supporting the equations describing the flow motion and heat transfer. Hence, mesh quality and accuracy bear direct implications on the credibility of your simulation results.
Understanding the key role of mesh quality, we've designed an automated meshing procedure into our ColdStream software. To fully appreciate this feature, let's first get familiar with the foundational meshing techniques and the concept of aspect ratio in meshing.
Meshing Techniques: Block Mesh and Conformal Mesh
Two frequently employed techniques in the domain of CFD simulations are block mesh and conformal mesh. Both of these techniques have unique attributes and advantages, making them suitable for different types of simulations.
Block mesh, also known as structured mesh, consists of regularly shaped grid blocks that cover the computational domain. Each block typically comprises a regular arrangement of quadrilateral or hexahedral elements. Block meshes are easy to generate and can efficiently handle uniform or structured geometries, but they may struggle with complex or irregular geometries.
In a block mesh (Fig. 2), each block corresponds to a portion of the physical model, allowing for greater flexibility in capturing geometric details. The division of the domain into structured blocks also permits easy control over the distribution of grid points, aiding in maintaining the mesh quality and resolution where it matters most.
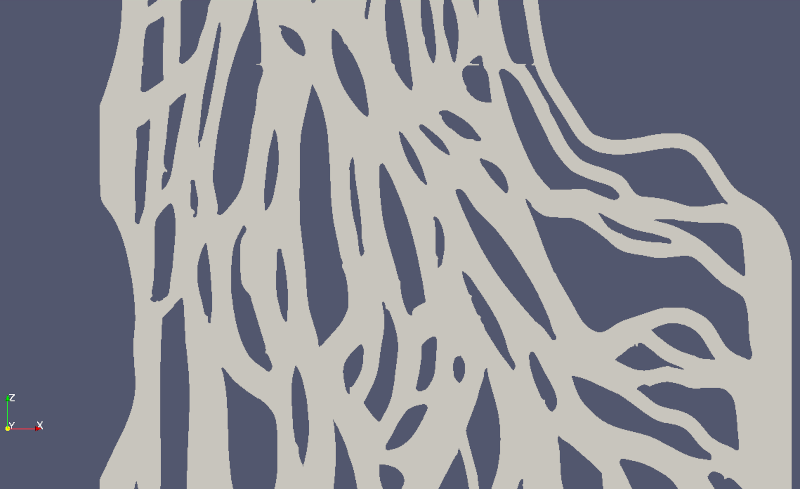
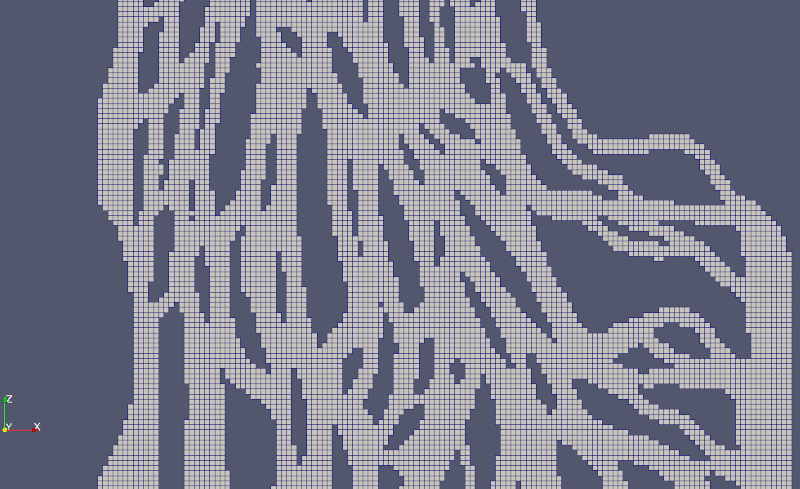
Conformal mesh, on the contrary, constructs a mesh that closely 'snaps' or conforms to the domain boundaries. This technique shines when it comes to capturing intricate geometrical features accurately and ensures that the pressure field calculated on the mesh is much more reliable. The conformal mesh methodology is adaptable when the simulation needs to adhere to the precise surface shape.
Conformal meshes are unstructured and possess the flexibility to conform to complex geometries with high fidelity. This can result in a more accurate representation of the model and, thus, more reliable simulation results. For instance, the pressure field calculated on a conformal mesh tends to be more reliable, as it avoids the artificial angles and jumps that are often present in block meshes, which can result in an overestimation of the pressure field.
.png)
Understanding the Aspect Ratio in Mesh
The aspect ratio in a mesh is a key metric that refers to the ratio between its longest and shortest dimensions. This ratio can considerably impact the stability and accuracy of a simulation.
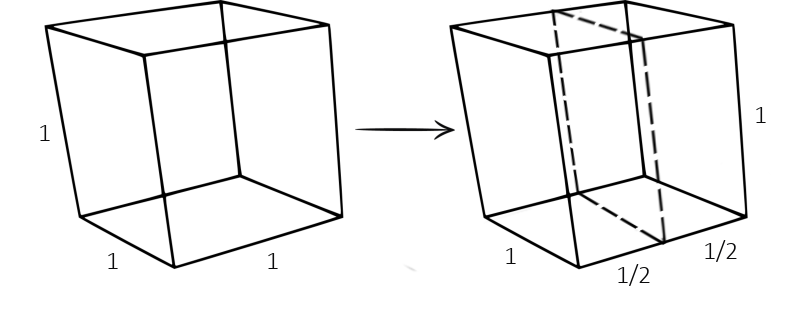
Mesh elements with an aspect ratio approaching 1, indicating their close resemblance to cubes, offer enhanced efficiency in solving equations and improve the accuracy of simulation results. Nevertheless, it is important to note that this approach may not be universally applicable.
In specific scenarios, for example, in boundary layer simulations, having elements with higher aspect ratios could be desirable. These slender elements can more effectively capture rapid changes in flow and temperature fields, which are characteristic of boundary layers. The ability to fine-tune the aspect ratio based on the simulation needs makes it a critical factor in meshing.
In cases involving cold plates or similar configurations, it is also desirable to increase the aspect ratio in order to avoid exploding the cell count with too many details in less relevant situations, as illustrated in Fig. 2.
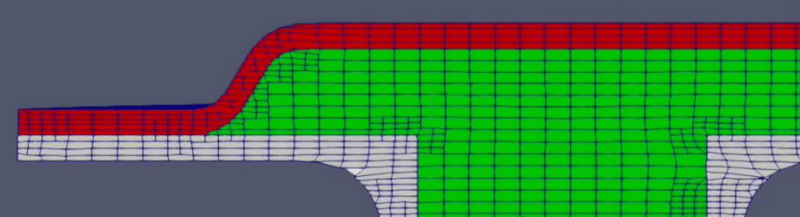
ColdStream Advantage: Automatic Meshing
Incorporating the principles of the meshing techniques, ColdStream has an integrated automated meshing procedure that brings accuracy, reliability, and efficiency to your projects. The automation ensures that the mesh quality is high and represents the model's geometry accurately.
One of the most significant advantages of automated meshing in ColdStream is productivity. Unlike manual meshing, which can be time-consuming and challenging, especially for complex geometries, ColdStream's automated procedure generates the mesh in minutes. This allows for faster design iterations, quicker product development, and more efficient utilization of resources.
ColdStream's automated meshing procedure guarantees consistency across different simulations of the same problem. It enforces quality standards such as element size and shape, ensuring accurate simulations. By providing high-quality mesh elements, the software also improves computational efficiency, enabling the analysis of more intricate models.
Cost reduction is another major benefit of automated meshing in ColdStream. Manual meshing can be costly, requiring specialized expertise and hours of labor. ColdStream eliminates these labor costs and frees up resources, making your projects more cost-effective.
The automatic meshing procedure in ColdStream offers a robust solution for achieving efficient and accurate CFD and thermal simulations. It enhances productivity, ensures consistency, improves accuracy and quality, and reduces costs. This ensures that your simulations are fast, accurate, and reliable, leading to a more efficient product development cycle.
Experience the robustness and accuracy of ColdStream's automated meshing process. Request an interactive demo here.
‍