Moore's law states that the number of transistors doubles every two years. This fact results in a continuous increase in volumetric heat production. Designing the cooling system becomes more complex, and sticking a finned heatsink on the component is no longer sufficient in high-end e-motors, EV batteries, power electronics, etc. Thermal engineers are now required to create extremely efficient cooling systems.
A cooling system can be conceived using two design strategies. The initial approach is entirely manual. The manual design process involves several steps, such as defining the design objectives, creating a rough design, using simulation tools to evaluate thermal performance, and making adjustments. This process can be time-consuming and prone to errors.
The second approach combines AI and machine learning techniques with advanced design approaches, such as generative design and topology optimization. This approach involves defining the following input parameters: thermal performance requirements, material properties, and size and shape. Using these input parameters, the generative design tool generates multiple design options, which are then evaluated using simulation tools to identify the optimal design that meets the thermal performance requirements. The final step is to optimize the design further. This procedure automates the design process and reduces time and effort, eliminating human errors.
This blog post details how an AI-powered generative design tool, ColdStream, can significantly reduce engineering time. Let’s go over more details about each one of the approaches.
Manual Approach
The s-shaped or dimple-design heat sinks are the most widely used conventional method for cooling. This traditional design process is manually iterative, requiring multiple modifications, such as changing the channel size, length, or number of channels to optimize performance. Simulations evaluate each iteration, determining the optimal design and balancing factors (temperature, pressure, and manufacturability). Consequently, this approach can be time-consuming and costly.
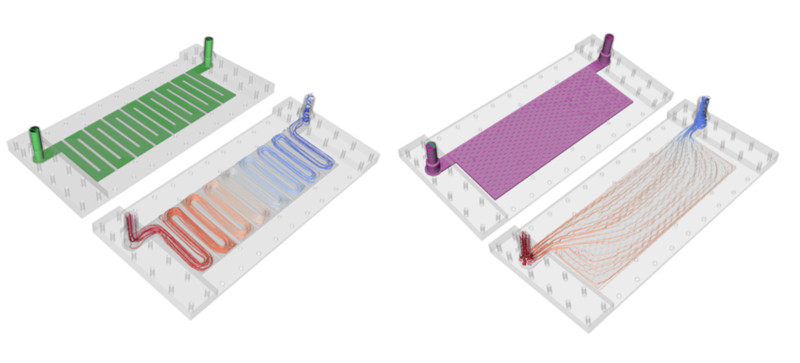
Generative Design Approach
Generative design tools have revolutionized engineering by reducing time and effort in designing and optimizing complex systems. These tools use algorithms and computation to automatically generate design options from inputs, constraints, and objectives. A notable example is aerospace structure optimization, which used to take months or years but now can be done quickly and automatically. Generative design has been effective in other industries, such as automotive and medical, optimizing structures and achieving lightweight design. Diabatix stands out as the only company using this approach for the thermal engineering process through our ColdStream software.
The process for designing and optimizing thermal products like heat sinks is similar to other engineering fields but with thermal performance as the specific objective. The first step is defining input parameters like material properties, operating conditions, design region, desired thermal performance, and manufacturing method. Then, the generative design tool generates a design that meets specific requirements like size, shape, cooling channel number, size and location, and manufacturing method. The design's performance is evaluated using simulation tools, and the best option is chosen and further optimized. This optimization can include small design adjustments and running computer simulations several hundred times to achieve the highest thermal performance while meeting design and manufacturing objectives.
We name this approach a custom design. Let's examine one example.
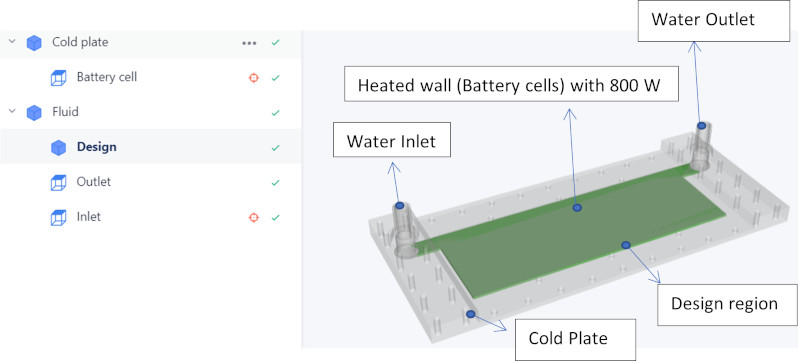
A case typically consists of several entities. Consider a basic water-cooled heatsink as an example. This heat sink has an aluminum base which should contain cooling channels. The aluminum plate's surface is treated with a heat-producing element. The constraints are:
- The different materials
- The fluid type
- The location of the inlet and outlet
- The location of the heat sources
- Design region (the domain in which cooling channels can be generated)
ColdStream algorithm uses a generative design methodology and topological optimization techniques to generate organic structures while simulating thermal performance. Through iterative cycles of material removal and redistribution, the algorithm optimizes the distribution of material to enhance heat transfer, repeating this process several hundred times until the final design satisfies specified constraints.
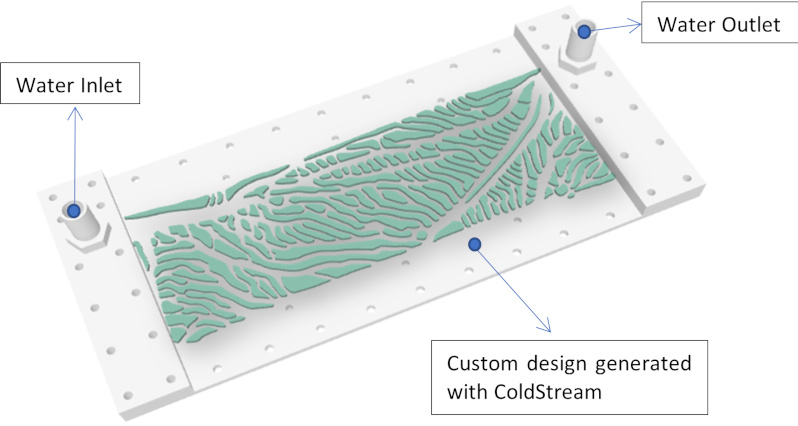
ColdStream offers a distinct advantage through its ability to optimize thermal products while simultaneously generating a manufacturable design compatible with various manufacturing methods, i.e., CNC milling, die casting, sheet metal forming, and 3D printing. Additionally, ColdStream features an efficient solution methodology by providing an estimated completion time and delivering the final design and accompanying CFD simulations. Upon completion, the results are available in downloadable Design STEP files and various forms of visual representation, including graphs, pie charts, tables, and fluid flow streamlines.
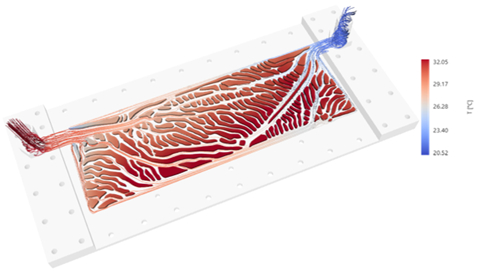
It is also interesting to point out that it is possible to visualize or download the results of all the other iterations by selecting the iteration number in design evolution.
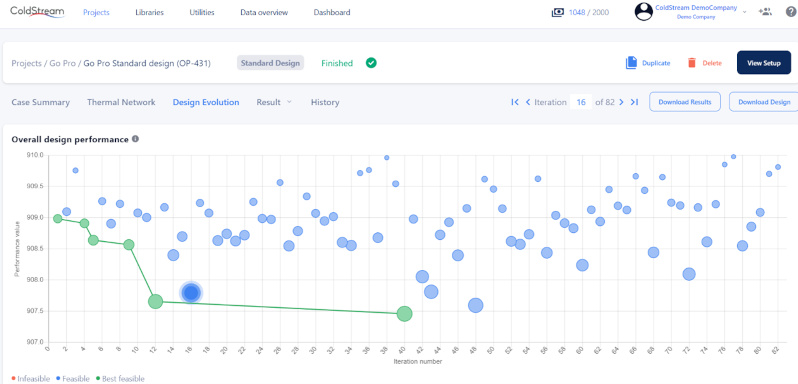
Using ColdStream prevents laborious manual design optimization for improved thermal performance. Thermal engineers can conserve time and resources by eliminating the need to repeat the design, simulation, and optimization process cycle. ColdStream, an AI-driven automated optimization process, can generate the most efficient solution without requiring further simulation. The results are readily available for visualization or download.
If you want a closer look, read more about battery cooling design here and request a free demo with our sales team.