Power inverters convert direct current (DC) to alternating current (AC) and are therefore crucial components. However, their compact size and high power density often leads to overheating, leading to reliability issues. Liquid cooling is one of the common solutions for power inverter cooling, but designing such a system is far from straightforward.‍‍
The thermal design process traditionally involves a labor-intensive cycle:
- Initial Geometry: Start with an empty design.
- Cooling Solutions: Incorporate known cooling features, such as pins or fins.
- Simulation: Perform computational or experimental testing.
- Analysis: Review performance and iterate until acceptable results are achieved.
This iterative process is time-consuming, often missing the global optimum solution.
That's why engineers often rely on generative design to solve their design challenges. Generative design uses an algorithm-driven approach that excels in exploring a high number of design possibilities and guiding engineers to optimal solutions.
Generative design utilizes algorithms to explore all potential configurations, represented graphically. On a performance graph:
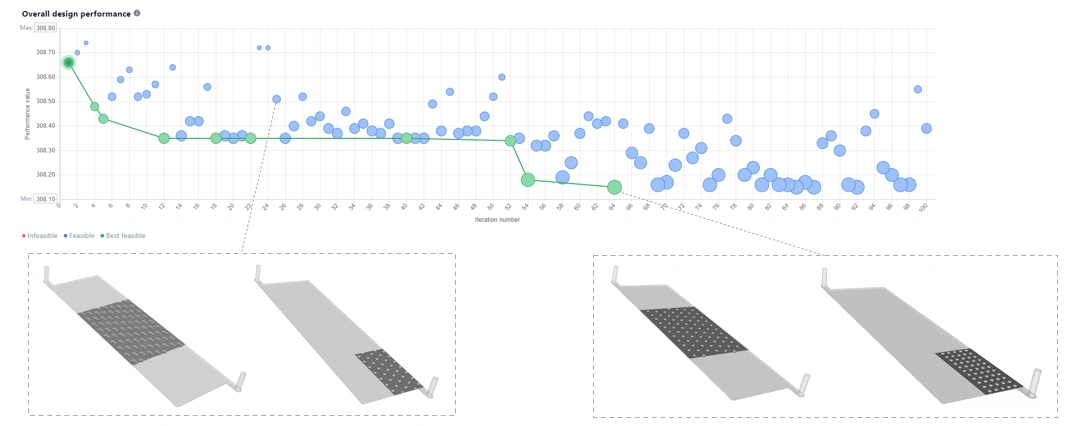
- The x-axis represents all possible designs (e.g., pins, fins, organic structures).
- The y-axis shows performance metrics (e.g., temperature reduction, thermal uniformity).
The key challenge? Engineers don't know what the optimal design curve looks like beforehand. Generative design bridges this gap by rapidly generating and evaluating multiple concepts.
Concept Phase
During this phase, the software generates diverse configurations based on:
- Material: For example, testing the suitability of a aluminum versus copper.
- Manufacturing Techniques: Comparing flexibility (3D printing) with cost-effectiveness (die casting).
- Structure Types: Pins, fins, and intricate channel designs are tested.
This stage narrows down feasible solutions that align with thermal requirements and practical constraints.
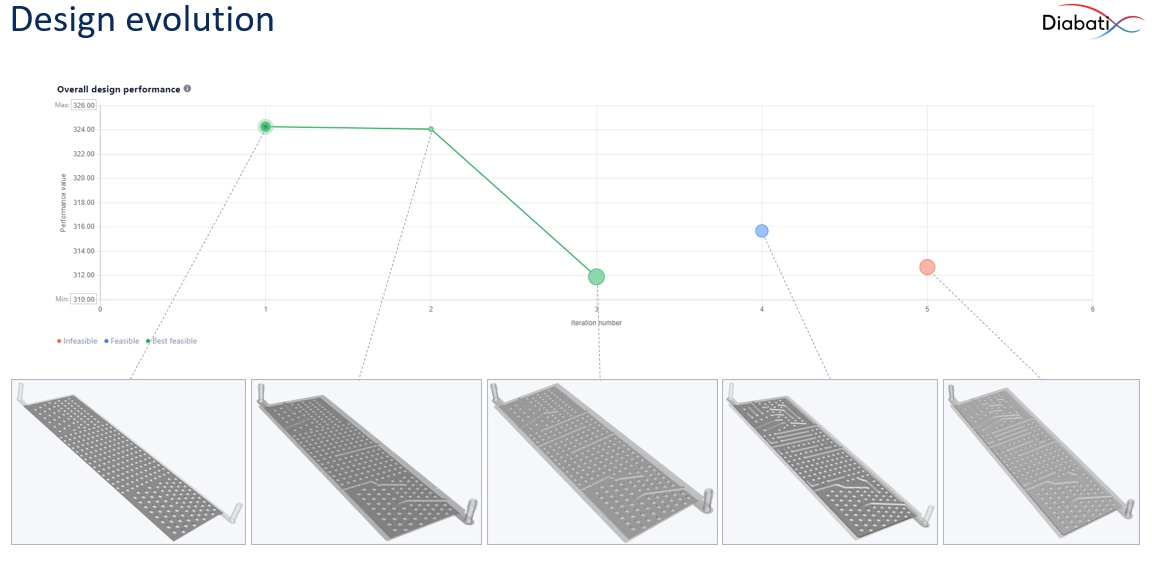
Custom Design Phase
After concept generation, generative design fine-tunes the most promising configurations. It incorporates detailed manufacturing and material constraints to ensure realistic and efficient designs. For example:
- Restricting channel dimensions to prevent structural deformation.
- Ensuring mold-friendly geometries for die casting.
Let's see how it looks like in practice.
Case Study: Double-Sided Power Inverter Cooling
For a real-world application, let’s consider a double-sided power inverter featuring:
- 90 heat-generating chips (top and bottom) producing over 4 kW of energy.
- Copper heat spreaders to distribute heat efficiently.
- Aluminum housing with liquid cooling (9.5 L/min flow rate of hydro-glycol).
The goal? Minimize temperature and maximize uniformity while maintaining practical pressure levels. Generative design plays a pivotal role here.
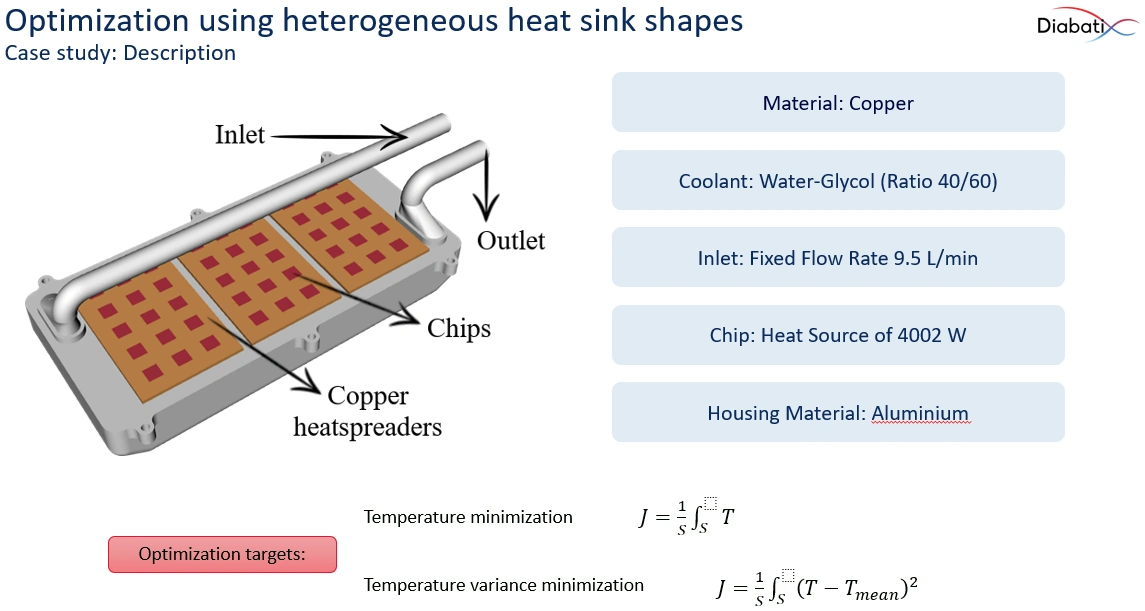
Steps in the Optimization Process
- Set Parameters in ColdStream: Engineers provide input geometry, material properties, coolant details, and performance goals into ColdStream.
- Concept Generation: ColdStream explores standard cooling solutions like pins or fins with variations in pin density, height, and arrangement, and materials (copper or aluminum).
- ColdStream rapidly evaluates configurations, identifying efficient designs for further refinement.‍
- Design Evolution: As iterations progress, designs improve.
Final Design Insights
Generative design produced intricate cooling channel patterns that maximized heat dissipation and uniformity. In some cases, the system created “spaghetti-like” 3D cooling channels, optimized for additive manufacturing, demonstrating the flexibility of this approach.
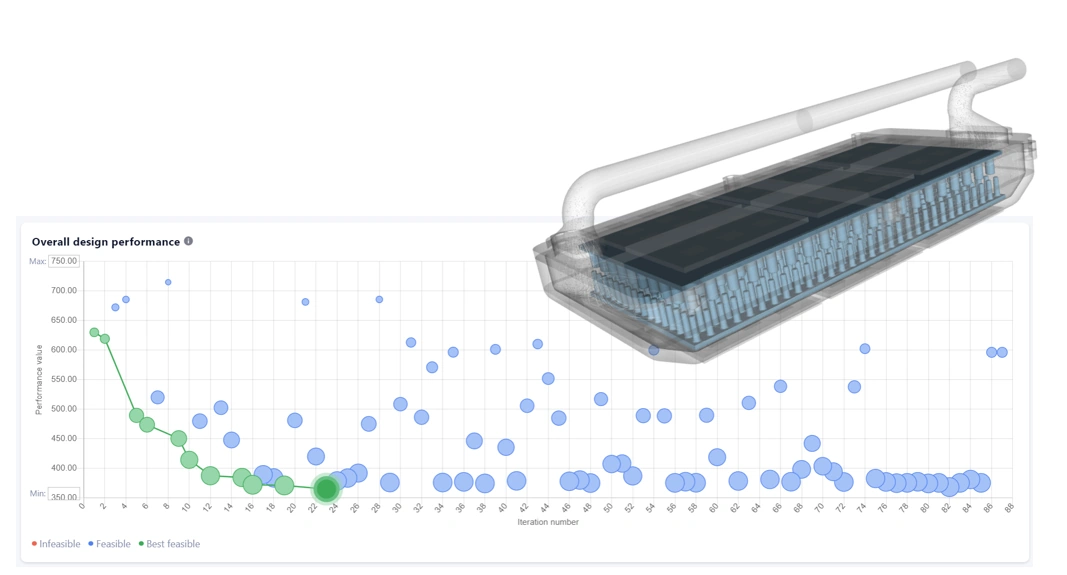
Advantages of Generative Design
Generative design increases efficiency by automating design exploration, enabling engineers to evaluate hundreds of configurations in hours rather than weeks. These designs almost always surpass conventional solutions in thermal efficiency and uniformity as well. By factoring in material costs and manufacturing constraints from the outset, generative design ensures that the final product is not only high-performing but also cost-effective and production-ready.
Conclusion
The complexity of power inverter cooling necessitates innovative solutions, and generative design is proving to be a transformative tool. By automating the design process and optimizing performance, tools like Diabatix’s ColdStream enable engineers to overcome thermal challenges with unprecedented efficiency.
Whether you're designing power inverters, high-performance electronics, or any thermal-critical application, generative design is a step forward in achieving the perfect balance between functionality, efficiency, and cost.
Are you ready to redefine your approach to thermal design? Explore the potential of generative design today!
‍