Triply Periodic Minimal Surfaces (TPMS) are complex geometric structures with surfaces that repeat smoothly across three dimensions. These surfaces are defined by a single implicit function and have transitions between their repeating units, making them suitable for stress, fluid flow, and heat transfer applications. Some common TPMS forms include gyroids, Schwarz surfaces, and diamond and linoid patterns, each offering unique thermal properties.
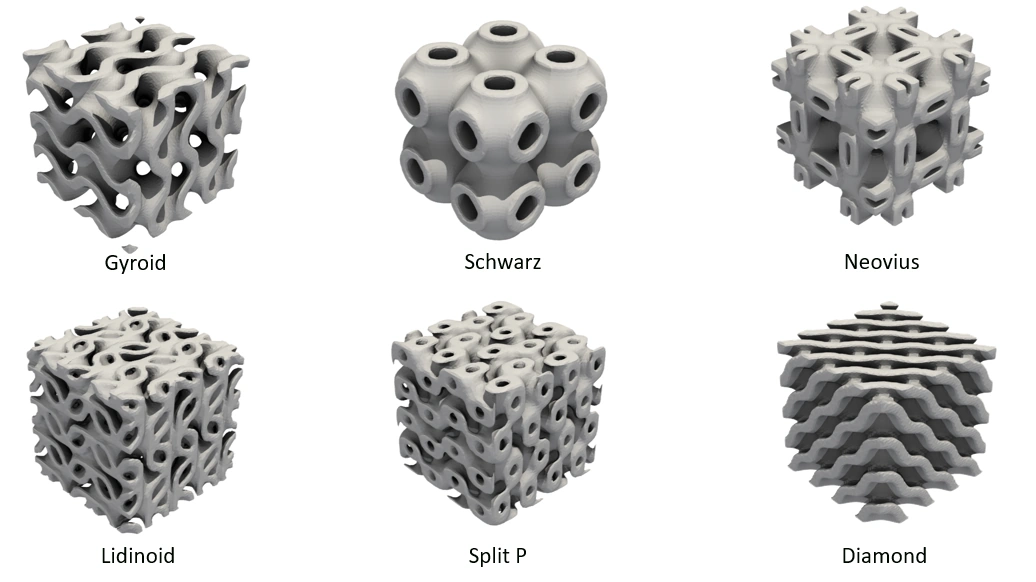
Gyroids, for example, are known for their high surface-to-volume ratio and open lattice structure, which encourages fluid mixing—a key factor for effective heat transfer. With a low thermal resistance comparable to traditional heat-dissipating structures, TPMS elements have emerged as a promising design strategy for maximizing heat transfer while maintaining compact, highly efficient thermal solutions due to the following characteristics:
- Low Thermal Resistance: TPMS surfaces facilitate heat dissipation.
- Enhanced Fluid Mixing: The geometry lessens fluid boundary layers.
- High Surface-to-Volume Ratio: With an extensive contact area for fluid interaction, TPMS geometries make optimal use of available space for thermal exchange.
However, TPMS designs are not without their own set of challenges. Their dense structure can lead to increased pressure drop, and their complex shapes typically require additive manufacturing, which limits material options and can increase production costs.
Optimizing TPMS Structures in the Design Process
Given their intricate nature, TPMS structures lend themselves well to parametric studies, where control variables (such as size, spacing, and thickness) can be iterated to find the best-performing configurations. While parametric studies enable fine-tuning of these designs, they also demand computational resources, as each iteration requires re-meshing and shape adjustments. To simplify this process, Diabatix developed a unit cell approach that breaks TPMS structures down into repeatable elements. By focusing on a single unit cell and iterating fewer variables, such as cell size, shape, and thickness, engineers can efficiently test a broad range of configurations without overwhelming computational demands. This method not only speeds up optimization but also reduces the complexity involved in working with TPMS geometries.
Using Implicit Modeling for Efficient TPMS Design
Another key aspect of TPMS design is the use of implicit modeling. Unlike traditional 3D models that represent surfaces with triangles or patches, implicit modeling represents complex geometries using mathematical functions that define surfaces implicitly as level sets of equations. This approach allows engineers to simplify boundary detection and carry out Boolean operations more easily, facilitating efficient manipulation of TPMS structures for thermal applications. For example, a gyroid shape—known for its high surface area and self-supporting structure—can be represented as a simple equation within the unit cell approach. This significantly reduces the model’s computational requirements, enabling engineers to test multiple configurations without sacrificing detail or accuracy. Implicit modeling improves the process by making it easier to combine structures, assess geometric boundaries, and optimize designs with high-resolution precision.
Real-World Applications of TPMS in Thermal Management
TPMS structures are being successfully implemented in various thermal applications, from CPU cooling to heat exchanger optimization. Here are a couple of practical examples:
- Liquid-Cooled CPU Heat Sink: In a commercial CPU heat sink, different configurations—using TPMS gyroids, traditional pins, and fins—were evaluated for temperature management. The gyroid structure achieved a balanced temperature distribution across the heat sink, while traditional pins and fins maintained lower peak temperatures in specific areas. These results highlighted the importance of application-specific design choices, with TPMS proving effective under nominal flow conditions, but with limitations when flow rates varied.
- Air-Cooled Heat Sink: For an air-cooled application, a heat sink was optimized using TPMS, pins, and fins. While the gyroid configuration provided a dense structure, it restricted airflow more than pin and fin designs. Pins and fins, on the other hand, allowed airflow to pass through more freely, making them better suited for applications where airflow constraints were critical. This example reinforces that while TPMS can offer superior thermal performance under certain conditions, traditional designs still have advantages in specific applications.
Key Takeaways
TPMS structures offer a powerful tool for thermal management, with benefits including low thermal resistance, improved fluid mixing, and a high surface-to-volume ratio. However, as these case studies show, the effectiveness of TPMS structures depends on the application’s specific needs, such as flow rate, pressure requirements, and manufacturing constraints. By leveraging Diabatix’s ColdStream platform, engineers can explore, optimize, and implement TPMS structures in their designs, maximizing thermal efficiency while minimizing computational demands. With innovative techniques like the unit cell approach and implicit modeling, TPMS structures can be explored and optimized efficiently, paving the way for advanced, high-performance thermal solutions.