Generative design, topology optimization, and parametric optimization have become increasingly popular. But what do those terms mean? Are they synonyms, and can they thus be used interchangeably? Or is there a clear difference between them?
This blog post aims to answer those questions simply and understandably without getting deeper into the technologies.
What are the key differences between these terms?
Let’s start with the definition of generative design:
“Generative design is a design exploration process. Designers or engineers input design goals into the generative design software, along with parameters such as performance or spatial requirements, materials, manufacturing methods, and cost constraints. The software explores all the possible permutations of a solution, quickly generating design alternatives. It tests and learns from each iteration what works and what doesn’t.” [1]
Next, we’ll move on to the definition of topology optimization:
"Topology optimization is a design process that optimizes material layout and structure within a given 3D geometrical design space for a defined set of rules set by the designer. The goal is to maximize the performance by mathematically modeling and optimizing for a predefined set of targets." [2]
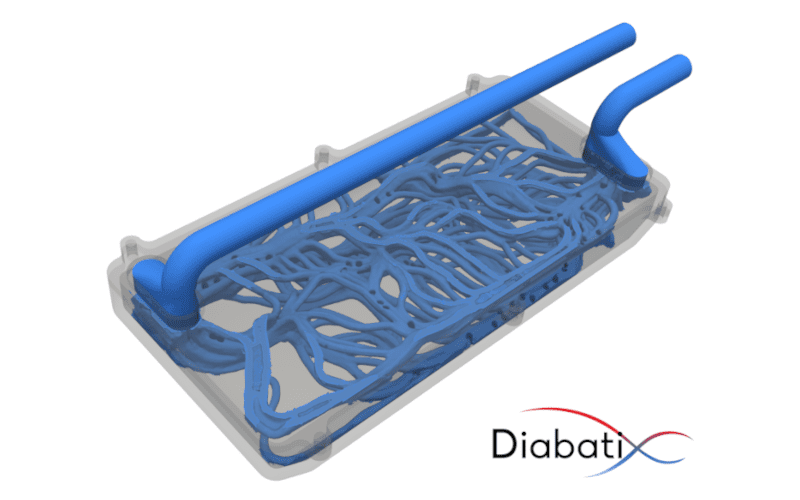
And finally, we conclude with the definition of parametric optimization:
Parametric optimization is a design process that optimizes the defining parameters of an already predefined material layout and structure. The goal is to maximize performance by modifying the defining parameters and measuring their impact on the predefined set of targets.
In essence, generative design is an umbrella term that describes several technologies, while topology and parametric optimization are some of the technologies.
A closer look into topology optimization
From the definition of topology optimization, the algorithm will return a material layout that optimizes the mathematical model of the underlying physical problem. There are multiple topology optimization methods, each with its ups and downsides. The most commonly used algorithms are the density-based approach and level-set topology optimization.
The density-based approach has the advantage that the density field is changeable throughout the entire design domain. New cavities and new structures can appear anywhere during the optimization run.
On the downside, there must be flow in the places marked as solid to have information in those areas. This brings additional modeling issues that can be reduced with some tricks. In this author's eyes, the density-based approach is the ideal algorithm to get a design from scratch. It also makes it very approachable to people without thermal experience since the design is completely computer-determined, and no initialization is needed.
On the other hand, level-set topology optimization keeps the fluid and solid parts separate. This approach reduces the modeling issues described in the previous paragraphs. However, as a consequence, one loses the information in the solid parts. Therefore, the standard level-set topology optimization cannot create new cavities or structures throughout the design domain - it will only reshape the edges of the fluid-solid interface.
Again, some tricks are available in the literature (like hole seeding) to get around this issue [3]. From the author's perspective, this makes it an ideal algorithm if it has a good initialization, for instance, a design coming from a density-based approach.
The two approaches mentioned above are the most commonly used methods for topology optimization. More advanced algorithms are available in the literature, depending on the complexity of the problem and the strategy that is more suitable to solve it.
Topology optimization methods are proving to return very effective designs for forced convective heat transfer and natural convection thermodynamics system components. In recent years, the available manufacturing methods limited the ability to manufacture extremely complex shapes. The recent development of newer methods of implementing manufacturing methods, such as die casting, CNC milling, and sheet metal forming, now allows for the consideration of highly sophisticated designs that were previously not possible.
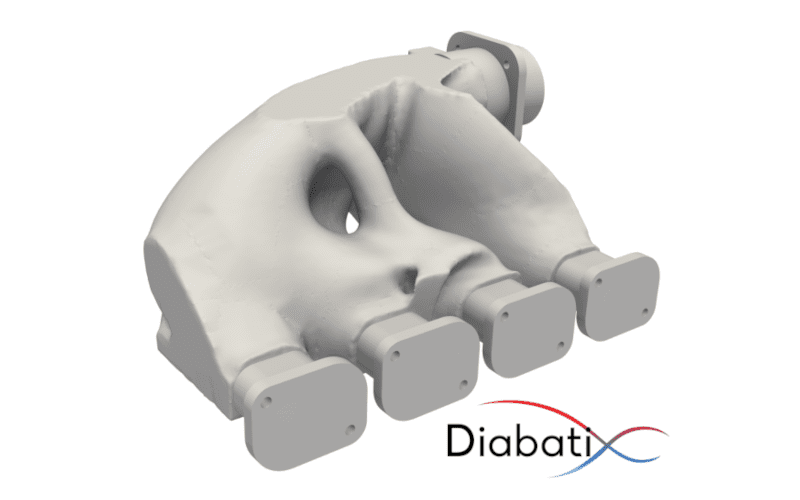
A glance into parametric optimization
The designer a priori dictates the general design philosophy applied to the model. For example, the designer can choose to have only pins or fins returned by the method. Thus, the optimization algorithm will subsequently optimize the defining parameters of those pins and fins (height, width, spacing, etc).
This optimization approach is quick and cheap, as only a few parameters can change. The designer also has full control over the type of design that will be returned and how it is manufactured. For instance, a topology optimization process will deliver a design that is fully custom to the specified problem and will require either an in-house manufacturing department or one needs to rely on third parties to manufacture the piece. With parametric optimizations, one can constrict the optimizer to consider off-the-shelf products solely.
This is the preferred method if the cooling requirements are more relaxed. However, as of late, classical pins and fins are increasingly more challenging in meeting the thermal performance criteria. Either the setup should change (forced convection instead of natural convection, another coolant, more exotic/expensive materials, … ), or one needs to consider going for a custom design using topology optimization.
Conclusion
Generative design, topology optimization, and parametric optimization are definitely not synonyms. Generative design is a wider term describing many design exploration technologies. In contrast, topology and parametric optimization are the technologies mentioned above. Topology optimization will return a design beyond human imagination, while the designer will a priori prescribe a giving design philosophy for parametric optimization runs.
Our software, ColdStream, generates custom designs through topology optimization. That's why the thermal and flow optimization process driven by ColdStream results in designs and performances beyond human imagination. Any change to the operating conditions can result in a completely different yet optimal design topology.
If you are more interested in buying off-the-shelf pin or fin heatsinks, ColdStream also offers parametric optimizations through its standard design mode. Consult more information here, and don't hesitate to contact us.
‍
References:
[1] https://www.autodesk.com/solutions/generative-design
[2] https://engineeringproductdesign.com/knowledge-base/topology-optimization/
[3] Xia, Q., Shi, T., & Xia, L. (2019). Stable hole nucleation in level set based topology optimization by using the material removal scheme of BESO. Computer Methods in Applied Mechanics and Engineering, 343, 438-452.