Integrated Circuits (IC) are a fundamental component of Central Processing Units (CPU), as they are responsible for executing the instructions of a computer program. The number of resistors in an IC Â grows double every two years as governed by Moore's law. The increasing number of resistors in an IC leads to an increase in heat generated that scales linearly with the number of resistors. In general, the amount of heat generated by a CPU depends on the computational requirements. The generated heat must be dissipated in order to avoid overheating, which can cause performance degradation and potential damage to parts.
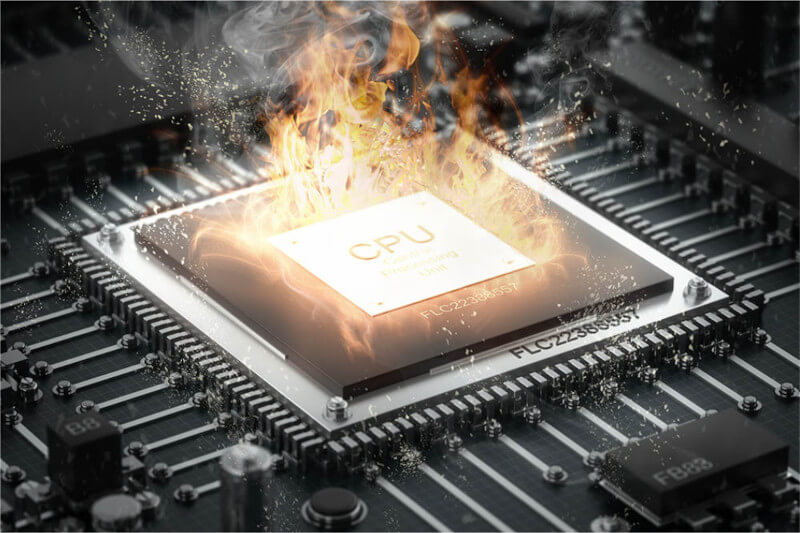
To maintain the optimal operating temperature in electronics, heat sinks are ubiquitous applications. Notably, heat sinks are heat exchangers that are integrated into electrical hardware to transfer the heat generated from a mechanical component to the surrounding. In most cases, the surrounding can be air or cooling fluid for highly computationally demanding processing operations. For a long time, heat sinks were manufactured with CNC machines. The design and development of heat sinks for long have been constrained by manufacturing processes and have not shown impactful advancement in performance until recent years.
Watch the on-demand webinar here
A game-changer: Additive manufacturing and Generative design
For more than a century, the products we design have been heavily constrained by the limited capability of manufacturing processes such as machining, molding, and casting. This has also been the case in the design and development of heat sinks. Because of manufacturing limitations, the pursuit to find innovative designs for high-performance heat sinks has faced hurdles. In recent years, additive manufacturing has showcased promising applications that can allow you to manufacture novel products on demand incorporating digital data in the manufacturing process. Â The progress made in additive manufacturing has enabled the reconsideration of generative design in creating highly efficient heat sinks without being limited by manufacturing constraints.
Generative design complemented with High-Performance Computing (HPC) and Artificial Intelligence (AI) is able to revolutionize the product development cycle by Computer-Aided Design (CAD) for digital modeling and Computer Aided Engineering (CAE) for virtual testing. This approach has significantly cut down the time and cost that are needed to deliver truly innovative products. Thermal management of electronic parts is one of the areas where generative design has been introduced to deliver novel heat sink designs for effective heat dissipation.
Challenge: Traditional design, analysis and manufacturing processes
In general, the performance of a heat sink is determined by the thermal conductivity of the material, working fluid flow rate, and geometrical characteristics of the heat sink. The geometrical design of heat sinks has been strictly constrained by the manufacturing process. The skived heatsink designs have the limitation where the geometrical features are fixed and the airflow can not be redirected for maximum heat dissipation, thereby not up to the task for next-generation CPUs. Recently Diabatix took on a challenge to utilize their ColdStream platform with the objective to develop high-performance heat sinks in collaboration with AMNOVIS, a Belgium-based additive manufacturing start-up.
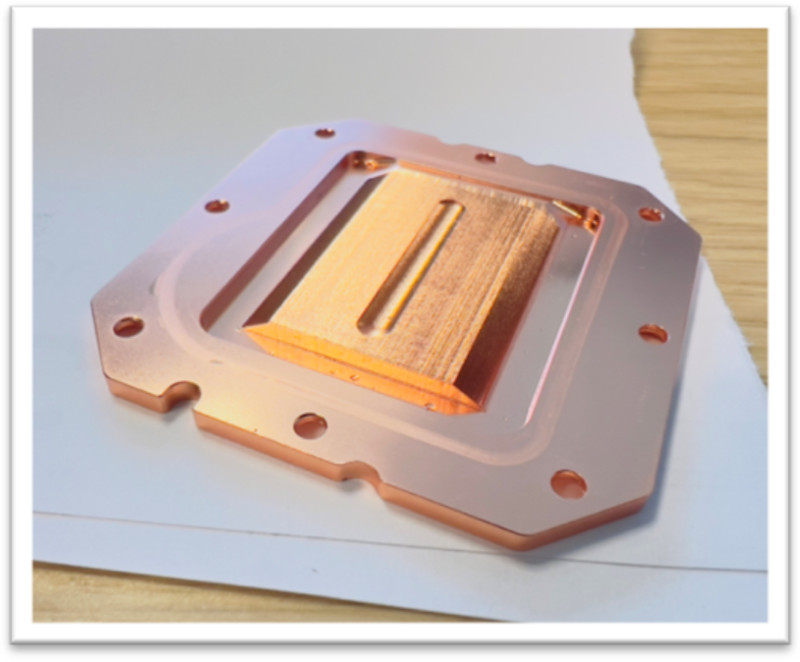
Solution: ColdStream by Diabatix
Diabatix is one of the leading companies specializing in this field to introduce AI-powered thermal analysis to thermal design tools through their ColdStream platform solution. ColdStream is a cloud-native generative design platform that runs using a standard web browser. Coldstream is an optimization and simulation tool where input geometrical data is analyzed with the physics of the problem to come up with new and innovative designs that satisfy the design constraints.
Case setup in ColdStream has a straightforward approach. The optimization process starts with uploading a geometrical model that defines both solids and fluid movement area of the heat sink. The dimension of the geometry is sized with respect to the CPU design and the housing components. Once the geometry is uploaded to the platform, setting up the boundary condition starts. In this stage, properties such as material properties, initial conditions, and constraints are set. The user also specifies the manufacturing setting, including the option for 3D printing. The minimum printed structure size is set depending on the 3D printer's capability.
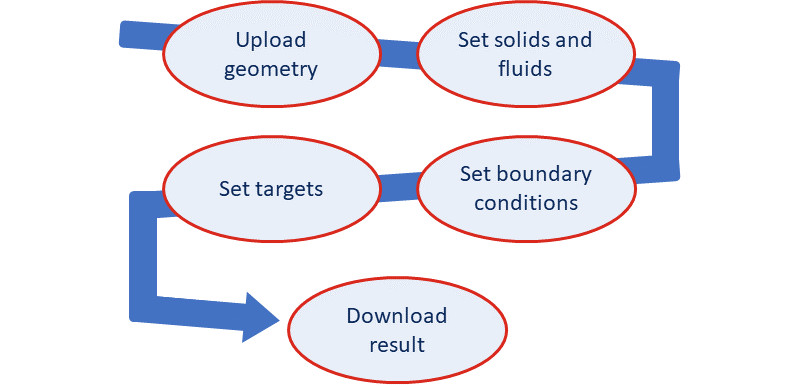
Once the preprocessing stage is completed the optimization process can be started. At this stage, all tasks are handled by the solver automatically in the background. Until a geometrical model that satisfies the constraints is obtained, the solver keeps iterating the geometry. When the solver obtains the optimal geometry for the predefined constraints, the iteration is terminated and the resulting file is available for post-processing. The CAD file then can be downloaded and sent to the manufacturer. Since ColdStream is equipped with both a simulation and optimization tool, the results from different scenarios are available for comparison.
In this case study, a base processor used is the intel I700 processor. The solver was provided with the base CAD model shown below. A heat flux of 250 W generated from the CPU was assigned as a heat load boundary condition. A temperature minimization objective was assigned to the heat generating surface. For the coolant, a water-glycol 40/60 mixture was used as a working fluid with a flow rate and temperature of 0.82 l/m and 40°C, respectively. The pressure loss was set to remain below 14 kPa between the inlet and outlet of the flow, the high-pressure loss target set aimed to avoid retrieval solution.
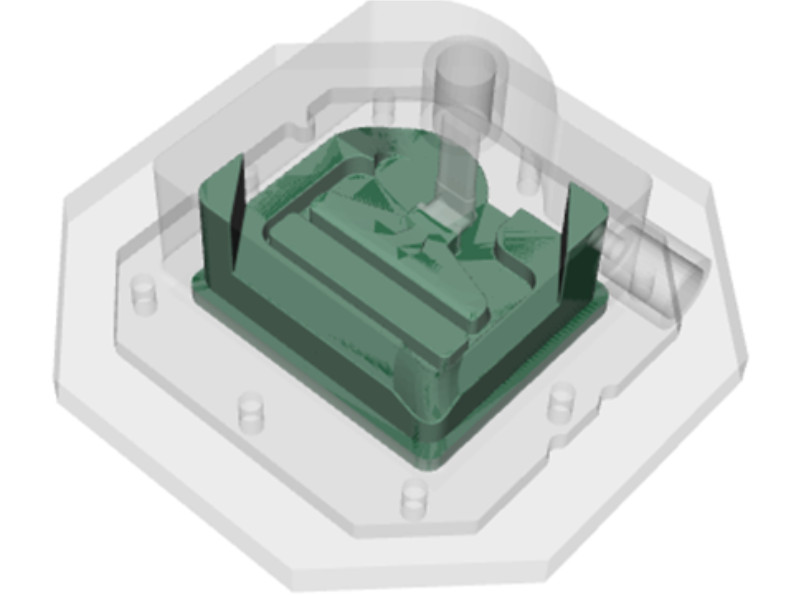
Result: Novel, Optimal & Manufacturable!
Using the provided information, ColdStream returned an optimized result geometry shown in Figure A. With the optimized heat sink design, the maximum temperature the CPU can reach is 56.4 C. The conventional skived heat sink design with the same heat load shows a maximum temperature of 76.14 C. The result is a 55% lower thermal resistance compared to the conventional design showing a potential to improve CPU performance and safety.
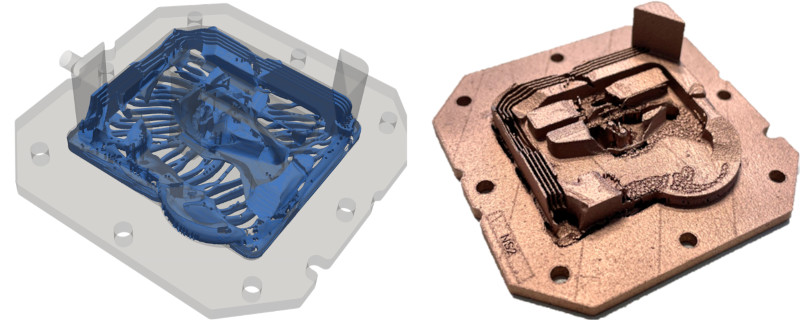
The primary concern when manufacturing generative designs with small structural sizes is to ensure the structural stability of the mechanical component. The laser powder bed fusion process has a narrow window for 3D printing copper components with the required properties. Using proprietary processes and technology offered by AMNOVIS, the design was 3D printed, as shown in Figure B.
An experimental investigation is already available in collaboration with KU Leuven to validate the simulation results - find more information here.
Explore the generative design possibilities here and do not hesitate to contact us to learn more about AI-generated heatsink solutions!