Did you know that some materials can conduct heat at different rates, depending solely on the orientation of the material itself? Materials that behave like this are known to have an “anisotropic thermal conductivity”. This refers to the property of a material to conduct heat differently in different directions, depending on its crystallographic structure, microstructure, or composition. In simple terms, it means that a material can conduct heat more efficiently in one direction compared to another.
In most engineering applications, thermal conductivity is typically modeled as isotropic, which means it is the same in all directions. However, in certain situations, such as when dealing with composite materials, textured materials, or materials with a preferred orientation, anisotropic thermal conductivity must be taken into account for accurate analysis and design.
Modeling anisotropic thermal conductivity can be complex, as it requires consideration of the material's unique properties. One common approach is to use tensors, which are mathematical representations that describe the relationship between the heat flux and the temperature gradient in each direction. Tensors are used to account for the anisotropic behavior of the material by defining different thermal conductivities along different axes or directions. This allows engineers to accurately predict the flow and heat transfer behavior in different directions and design systems accordingly.
The consideration of anisotropic thermal conductivity is useful in a wide range of applications. One example is in the design of electronic devices, such as computer chips, where heat dissipation is a critical factor. Anisotropic thermal conductivity can affect the performance and reliability of these devices, as the heat must be efficiently conducted away from sensitive components. By accurately modeling anisotropic thermal conductivity, engineers can optimize the heat dissipation pathways and ensure the efficient operation of electronic devices.
Another example is in the field of aerospace engineering. In spacecraft and aircraft design, anisotropic thermal conductivity is a crucial factor to consider due to the extreme thermal environments encountered. For example, during re-entry into the Earth's atmosphere, spacecraft experience high heat fluxes, and anisotropic thermal conductivity of the heat shield material can significantly affect the distribution of heat, potentially causing structural failure or damage. Accurate modeling of anisotropic thermal conductivity allows engineers to design heat shield materials that can withstand extreme thermal conditions and protect the spacecraft and its occupants.
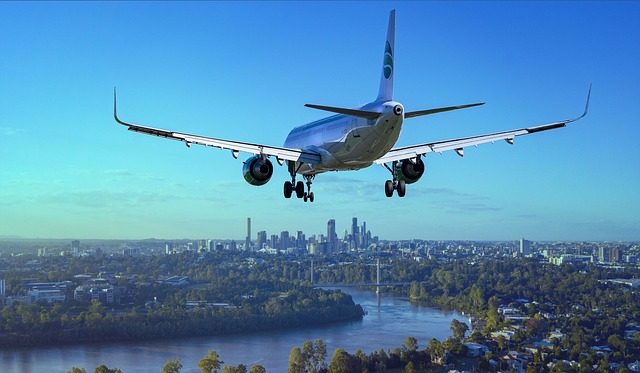
Furthermore, anisotropic thermal conductivity is also important in the field of materials science and manufacturing processes. For example, in additive manufacturing or 3D printing, the direction of heat transfer during the solidification of a material can affect the microstructure, porosity, and mechanical properties of the final product. Accurate modeling of anisotropic thermal conductivity can help optimize the printing parameters and ensure the desired material properties are achieved.
In summary, anisotropic thermal conductivity can play a significant role in influencing the physical behavior of flow and heat transfer problems. When defining a simulation or optimization problem, it is important to consider whether materials will display an anisotropic thermal conductivity or not, such that this is correctly reflected in the numerical representation of the problem. Accurate modeling of anisotropic thermal conductivity allows engineers to design systems and materials that can withstand extreme thermal conditions, optimize performance, and ensure the reliability of engineering applications.
Lastly, did you know you can easily define materials with anisotropic thermal conductivity using ColdStream? You can define it simply at the click of a button! All that you need to do is to define a new material, toggle the “anisotropic kappa” switch, and fill in the thermal conductivity value for each principal axis. Finally, once you save the new material, it is available to select for all your future cases. Your physically realistic case setups will be up and running in no time!
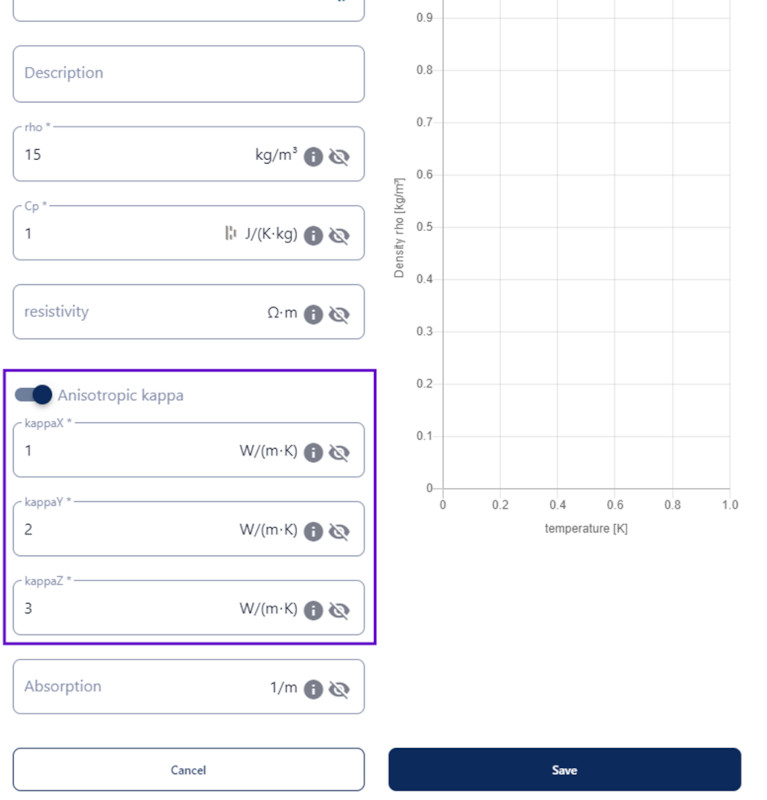
If you want to access how ColdStream can help with your workflow, please contact us here.