Generative design can have the stereotype of creating stunning exotic shapes and structures but then provide challenges once entering the prototyping and production stage. This can cause manual adjustments to the original generative design, causing unpredictable performance changes, which in the worst case, can lose the entire added value initially realized.
Here at Diabatix, we believe that generative design can always be manufacturable if executed properly. From the inception of our software ColdStream, it was clear that linking manufacturability to the very beginning of the design process is essential. While in the past engineers would create designs that are first thermally optimal to only later on figure out how they can be fabricated, ColdStream takes manufacturing constraints into account at the very beginning of any design creation. Before launching any new generative design run, the user is prompted to specify in detail the manufacturing limitation of their specific tooling. This allows us to proudly claim that designs delivered by ColdStream are fully manufacturable.
In addition, we wanted to build a tool that would adapt to all situations, knowing that not every engineering department has access to metal 3D printing or that it is simply not cost-effective for series production. For this reason, ColdStream hosts four main manufacturing types to allow for successful generative design for all applications: CNC milling, die casting, 3D printing, and sheet metal forming. So whether you are accustomed to 3D printing designs during prototyping or die casting for cost-effective series production, ColdStream will adapt to your preferred methodology and deliver designs that get the most out of manufacturing capabilities.
In a power inverter cooler use case, let’s discover how ColdStream takes manufacturability into account from the very setup of a new generative design and notice the difference in designs and performance when opting for different manufacturing types.
Cool, let’s check different manufacturable designs!
The first step in any generative design is defining the allowable design volume for the additional body to be generated within. The power inverter cooler is a liquid-cooled component with an in- and outlet on opposite sides and heat sources on the top and bottom faces (see Figure 1). The allowable design volume can be seen in Figure. 2. This volume will be filled by ColdStream with additional solid material to guide the channel structures to be optimal for conjugate heat transfer. Here ColdStream prompts you, as part of the case setup, to define the manufacturing technique you are using and, secondly, the specific constraints of your tooling.
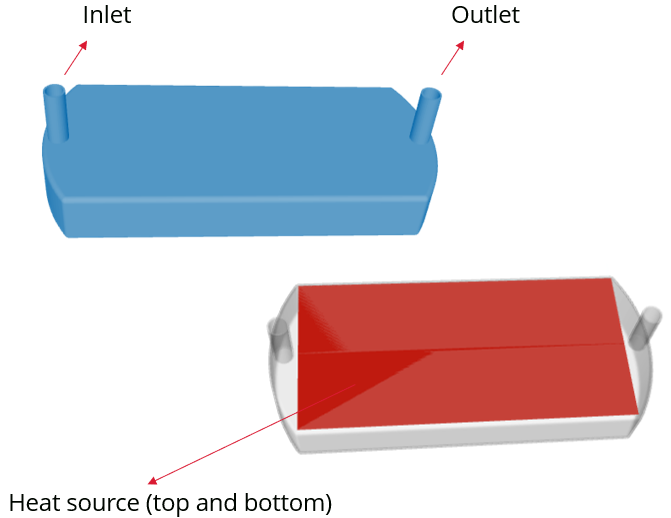
.jpg)
In the first instance of this optimization, metal 3D printing was selected with the smallest resolution size of 1.5mm. To ensure that every design made for 3D printing is fully manufacturable, the user has to define a set of constraints seen in Figure 3.
.png)
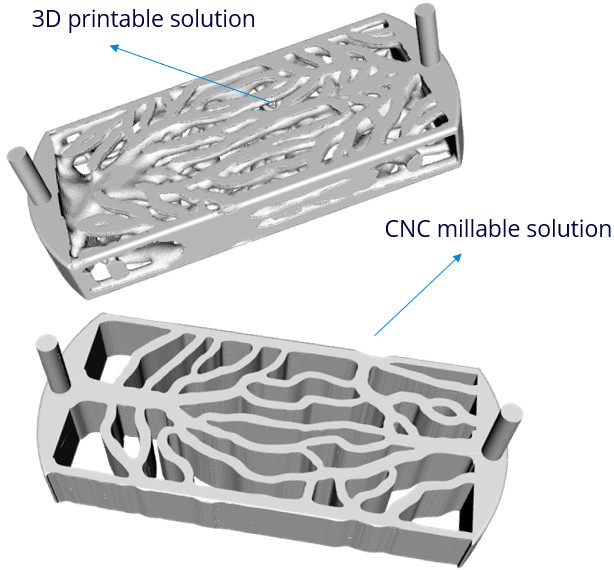
The key difference between the two designs is that 3D printing provides the most freedom for liquid channel designs, while CNC-milled designs will always be two-dimensional (Figure 5). The difference in the maximum temperature along the heat source is around 1 degree Celsius in favor of the 3D printing design.
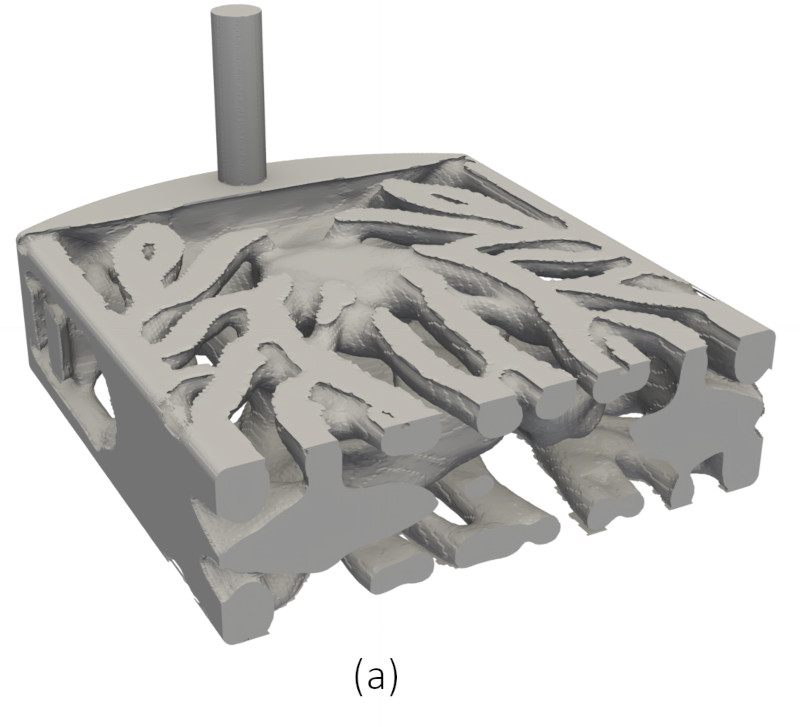
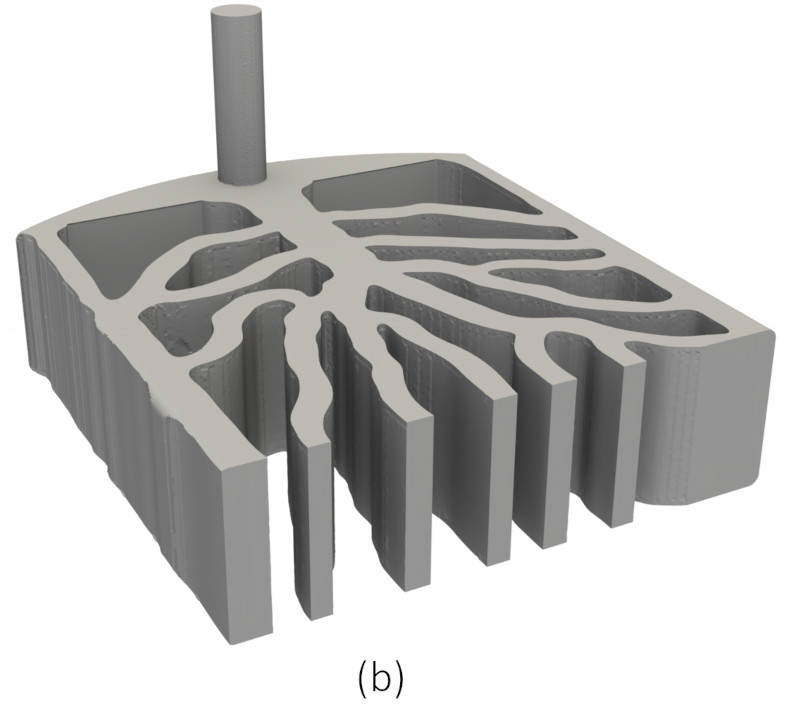
A quick overview of the performance benefit allows engineering managers to make informed decisions about where the performance gains are worth the increased manufacturing efforts. So whether you want to compare performance impact between different manufacturing constraints or see how far you can push the heat transfer with different 3D printing resolutions, generative design with ColdStream allows for convenient parallel design investigations.
Manufacturable designs - a reality
When generative design consistently delivers designs that have absolute certainty in manufacturability, it undoubtedly provides added value for any design or manufacturing division. Quality designs will have a direct correlation between simulation performance and real-life experimental performance; any simulated performance gains will translate to the manufactured part. Such trust allows for greater confidence to commit to AM toolchains. Simulation-driven design tools like ColdStream that incorporate manufacturing constraints to multi-objective optimizations enable engineering firms to get the most out of their manufacturing capabilities.
Explore the generative design possibilities here and visit our dedicated 3D printed heatsinks page. Don't hesitate to contact us for any further assistance!