Managing heat generation is a pivotal challenge for printed circuit boards (PCBs). As PCBs are not comprised of superconducting materials, they inherently resist electric currents, leading to inevitable heat production. This heat must be efficiently dissipated to maintain the functionality and longevity of electronic components. Understanding the fundamental paths through which heat escapes is crucial for optimizing PCB design and ensuring efficient thermal management.
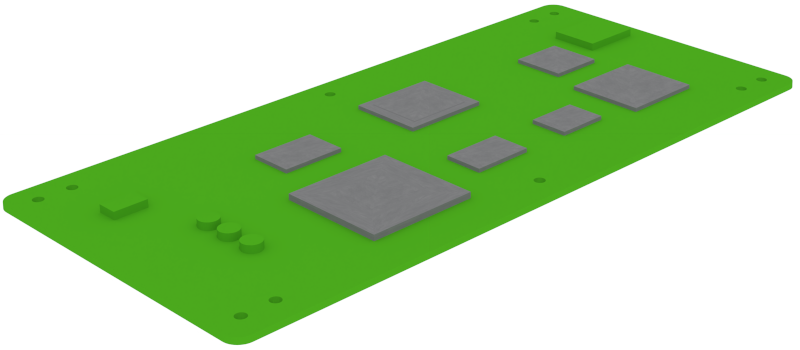
Today, we will navigate the three primary heat transfer mechanisms - conduction, convection, and radiation - and explore best practices for leveraging natural convection to enhance PCB cooling.
Understanding the heat transfer mechanisms
As we're aware, the materials used in PCBs are not superconductors; thus, electrical currents flowing through them encounter resistance. This resistance generates heat, which must be dissipated into the environment to prevent damage and maintain performance.
Heat can escape via three main pathways:
1. Conduction occurs predominantly in solid materials, where molecules are arranged in a fixed grid. Heat transfer happens as these molecules vibrate and interact, transferring energy from one to another. Conduction also occurs in fluid materials, but the movement of the molecules makes it less dominant. The material's thermal conductivity is a measure that prescribes how easily heat transfers from one molecule to the next; materials with higher conductivity facilitate heat transfer, allowing for a more uniform temperature distribution across the PCB. Enhancing conductivity can significantly improve heat dissipation from the chip to the board's other side.

2. Convection becomes the primary mode of heat transfer once the heat reaches the PCB's surface, moving through the housing to the air. In this process, fluid molecules, such as air, move freely, allowing them to absorb heat from the PCB surface and carry it away. The surface area influences convection's efficiency in contact with the fluid and the fluid's properties. This distinction highlights the dynamic nature of convection compared to the static behavior of conduction.
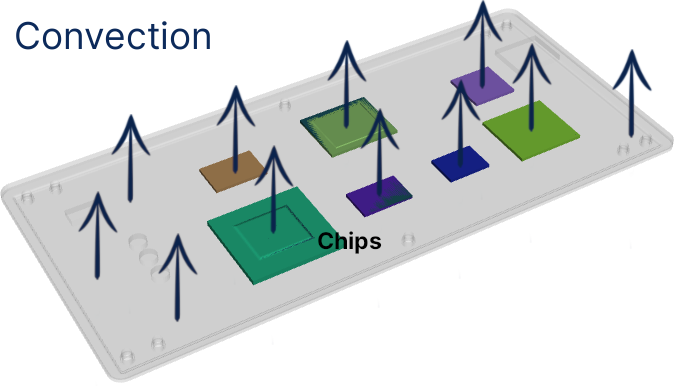
3. Radiation allows heat transfer without direct contact or a medium, utilizing infrared light. This mechanism is less relevant to PCB cooling under normal conditions, as it primarily occurs at very high temperatures.
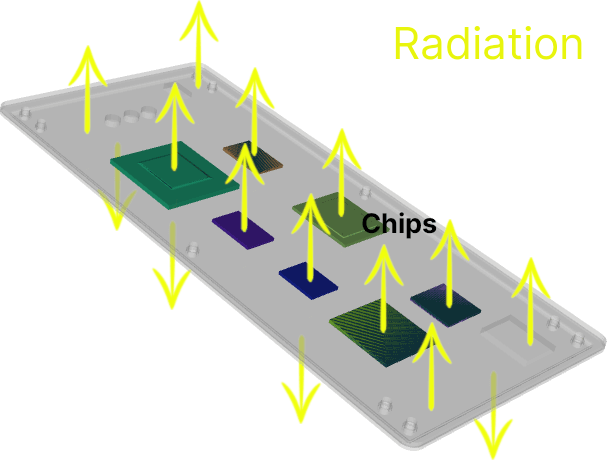
Natural Convection in PCB Cooling
Natural convection plays a vital role in PCB cooling, driven by the movement of heated air molecules. The efficiency of natural convection is significantly affected by the PCB's orientation and topology. A vertical placement of the PCB optimizes airflow and heat dissipation, as it reduces the area obstructing air movement. Positioning heat sources strategically on the PCB, away from obstacles like plugs, also enhances heat escape to the environment, adhering to best practices for thermal management.
Learn more about natural convection in PCB cooling
ColdStream generates heat sink concepts for PCB cooling. Using correlation-based simulations, ColdStream users are now able to deliver a broad range of different concepts for their design use case in a matter of hours. Although designs are still rudimentary, they provide the user with first insights into which cases' performance is expected to be best. This way you can cut the first guess step, allowing you to move faster and make better-informed decisions early in the design process.
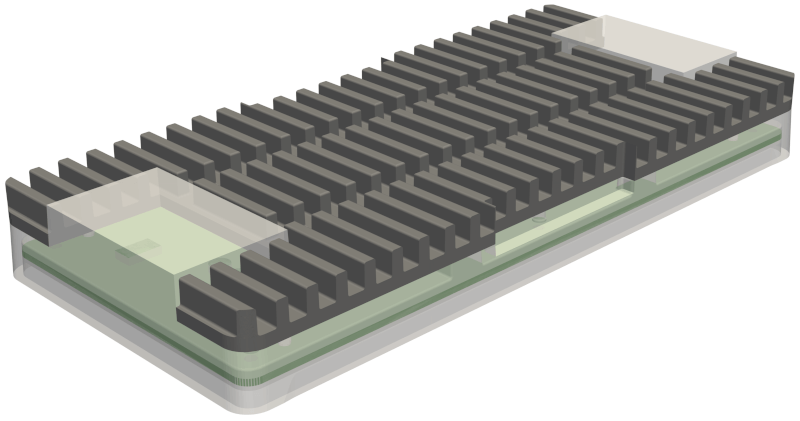
Sealing the deal on thermal efficiency
Effective thermal management in PCB design is critical for the performance and durability of electronic devices. By leveraging the principles of conduction, convection, and radiation, with a particular emphasis on maximizing natural convection, designers can optimize PCB cooling strategies. Understanding the impact of PCB materials, layout, and positioning can lead to significant improvements in heat dissipation, ensuring electronic components operate within their optimal temperature range. Embracing these best practices not only enhances cooling efficiency but also contributes to the advancement of more reliable and sustainable electronic solutions.